![]() | Studies in bibliography | ![]() |
From Chapter XIV (pp. 63-71), "Mill for making writing paper"
I come now to describe the mill for making this paper, which on Genoese
territory, and particularly at Voltri, reaches perfection. And to speak first of
the building and its fittings, I say that
the building should be in an airy locality and site, open to the north and
west winds, which are suitable for drying the sheets of paper quickly and
well, after they have been taken out of the water, and later, when they have
been sized.
the waters should be abundant and clear, with a good fall, so that they
have more force to work the stampers which beat the rags.[14]
the master mason should have previous experience of such buildings,
with respect both to the works in masonry, and to the wooden and metal
fittings.
The site of the building, which is of two storeys,[15]
is normally about 23-25
m long and 10 m wide.[16]
On the ground floor are placed the troughs and the
camshafts;[17]
the latter are connected to the wheels, which with the force of
the water make the stampers beat the aforesaid troughs.[18]
There is also a
chest 3.75-4 m long and 2-2.5 m wide, in which the rags are placed to rot, so
that they are easier to beat, and the chest is called the mettidore. Other containers
are needed, also of masonry, to take the rags after they have been
beaten. In another room on the same floor there is a vat, likewise of masonry,
5 m in circumference[19]
and about 1 m high, with a chest beside it containing
ready for use the material which has been beaten in the troughs, from which
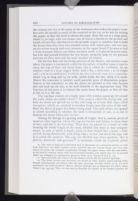
with the mould as much of the material to the vat, as he uses in making
the paper, so that the level is always the same. Near the vat is a large press,
about 2.5 m high, with two beams, one of which is buried in the ground and
stands on two feet, also buried in the ground, to give it stability; and to hold
the beams firm they have two wooden screws with metal pins, and two nuts
on the screws to grip and exert pressure on the upper beam.[20] As soon as half
a ream of paper, that is, 250 sheets, has been made, it is placed between woollen
felts and pressed between the two beams, using the nuts, by the physical
exertion of three men and the same number of women.
On the first floor are the living quarters of the Master, and another room
where the paper is burnished, called the lisciadore. A further room is used to
clean the rags of dust and shred them; this is called the crolladore. In yet
another room is a large copper boiler with a fire, a little over 1 m in height
and 2.5 m in circumference, in which the size is heated; near it is a container
about 1.25 m long and 75 cm wide, which holds the size, when it is made.
Above this container is another small portable press of dimensions proportionate
to the container; in this the sheets are pressed so that they become
soft and soak up the size, as we shall describe at the appropriate time. The
function of this press is to remove the water from the paper, so that all that
is left in it is the size.
The top floor consists of a single room with window openings all around
the walls, which are called rebatte.
[21]
The room is called the drying loft, and
here the sheets are spread out to dry and hung on certain thin ropes called
terragnine, which are attached to wooden frames near the eaves of the roof.
Here the sheets of paper dry before being sized. The said rebatte are opened
or closed according to whether the wind is favourable or not, so as not to
damage the sheets when they are wet.
Among the fittings is a grating made of trappe, that is, narrow pieces of
wood set close together, where the rags are beaten and shaken to clean them
of dust, and this is the first stage. Then they are placed on a bench or table
running the whole length of the room, divided into three or four compartments,
in each of which is fixed a piece of iron shaped like a hand, a little
curved, facing downwards, with sharp edges, to tear and shred the rags, and
it is called the squarcio. The rags are divided into three qualities, that is
fioretto, fiorettone and gruzzoto.
[22]
A workman called the studiente places
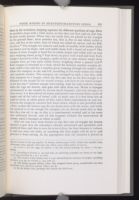
he sprinkles them with a little water, so that they can heat and rot and thus
be more easily beaten. When they are ready they are placed in the troughs
on the ground floor; these number ten, that is, five to one wheel, called a
cinci, and five to the other, four of which are called da repisto, and the fifth
da sfilato. [23]
The troughs are concave and made of marble, with insides which
are almost oval in shape, and each holds about half a barrel of water.[24] The
bottom of these troughs is lined for its whole length and width with an iron
sheet weighing about 50 kg,[25] kept firmly in place with wood and lead. Each
trough is beaten by three stampers, made of oak or some similar wood; these
stampers have 30 iron nails called biette, weighing about a pound each.[26]
Each stamper is attached to a shaft, which fits between another wooden element
called a key and has a wooden pivot running through the middle; this
allows the stampers to rise and fall, according as the water makes the wheel
and camshaft revolve. The stampers are arranged in such a way that, with
three stampers to a trough, when the first one rises in the first trough, it is
followed by the second in the second trough, and then by the third stamper
in the last one,[27] without anyone intervening. And the said studiente knows
when the rags are beaten, and goes and takes them out. Water is brought
continuously to the troughs by certain small channels, and even though it is
clean water, it is first placed in basins and passed over certain filters made of
copper and of the hairs of horses' tails, to make sure it is free from bits of
wood or straw, or other pieces of dirt, and it flows continuously in and out.
It leaves the trough by another hole lower down, which is also provided with
a filter, so that the beaten rags do not drain away with the water; and while
the material is in the trough the stampers are so cleverly made that as they
beat they also stir it up, so that it is continuously washed and at the same
time uniformly beaten; and all this happens without the intervention of
anyone, until it becomes as white as milk.
After the rags have been beaten in this first row of troughs the beaten
material is put into the containers already mentioned and sprinkled with
powdered lime, and thus it stays for several days; the lime foments it, reduces
it, and eats away the hairs, or anything else that might still be in it, and
prevents it from rotting. At the appropriate time the material is placed in
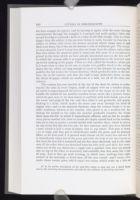
continuously through the troughs, it is purged and made perfect. After this
second beating it is placed a little at a time in the fifth trough. This is a little
bigger than the others; it has no iron lining or nails, because its function is
simply to dilute with water the beaten material which comes into it and
then stays there, but it has on the bottom a slab of millstone grit. The stampers
have no nails, but it is true that they are larger than the others, and as they
beat they dilute the material until it seems just like snow. It is straightaway
placed in the chest which we have already mentioned next to the first vat,[28]
to which the vatman adds it as required, in proportion to the material used
up in the making of the paper. There is a boy called the lavadore, whose job
it is from time to time to stir one or maybe two paddles fixed to the ceiling
above the vat, which are long enough to reach to the bottom; by moving the
paddles the boy makes the beaten material, which gradually sinks to the bottom,
rise to the surface; and thus the stuff is kept uniformly dense, so that
the sheets of paper, which are made one at a time, are all of the same consistency.
The vatman has two moulds of the size of the sheet he wishes to make,
exactly the same in every respect, made of copper wire on a wooden frame,
on which is superimposed the device and name of the owner of the mill. To
handle the mould he has another wooden frame, made like a picture frame,
which he puts over it; he then lowers it carefully with both hands, puts it in
the water and pulp of the vat, and then takes it out gradually and gently,
shaking it a little, which makes the water run away through the mesh of
copper wire, and so the material thickens; then the vatman hands it to another
workman, known as the coucher, who places it on a woollen felt. Inclining
the mould to the right the coucher gradually transfers the whole
sheet onto the felt, to which it immediately adheres, and on this he straightaway
places another felt; then he hands the empty mould back to the vatman,
who gives him in return a second mould with another sheet, which he places
on top of the felt like the first one. So they continue until they have finished
a post, which is half a ream of paper, that is, 250 sheets. This post is about
1.12 m high, and they put it immediately under the press, and by physical
effort, as we have said, it is pressed until almost all the water has run out. It
is immediately taken out of the press and with the help of the boy known as
the layer the first felt is removed and the first sheet detached, and in the same
way all the other sheets are detached from the felts with such skill, that sometimes
out of the 250 sheets not a single one is spoiled; then they are placed
one on top of the other so accurately and carefully that they seem like a bar
of soap. And so they go until evening, in which time, working from eight
o'clock in the morning—a fixed time, all the year round—until sunset, they
make about twenty posts, which equal ten reams, which make up a bale of
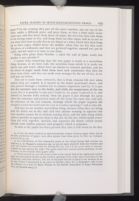
other, under a different press, and press them, so that a little more water
comes out, and they leave them there all night; the next day they take them
to the drying room to dry, and hang them on thin ropes; and so as not to
tear them they have to take five or six sheets at a time, which they then hang
up on these ropes, folded down the middle; when they are dry they seem
like pieces of cardboard, and they are gathered together, opened out, put in
a pile, and left until it is time to size them.
Sizing takes place from October 1 until the end of June; really hot
weather is not suitable.[30]
I cannot help remarking that the way paper is made is a marvellous
thing, because, as we have said, the materials from which it is made are
merely rags and water, which have no viscous or resistent qualities, and yet
the sheets of paper made from them have such consistency that they are
better than cloth, and they are made even stronger by the use of size, as we
shall now say below.
This size is made from carnuccio, that is from remains left over when
animal skins are tanned. It is heated in the boiler mentioned above, and
then poured through a woollen felt to remove impurities and fat. It is put
into the container next to the boiler, and while the temperature of the size
is such that it is possible to put one's hand in, the paper is placed in it, and
allowed to become fully soaked; then the paper is put through the press
above the container and pressed until all the water has come out, and only
the substance of the size remains, through which the paper acquires the
strength to resist the wind and the rain in window-openings,[31]
and to take ink.
And here we see another marvellous thing, because when they are being
sized the sheets are so dry and arid that anyone wanting to separate one
from another cannot do so without tearing them, and the only thing which
makes it possible to separate them is the size. So the size, which makes everything
else stick together, unsticks and separates the sheets—which occurs
through some hidden potency and property which it possesses.
As soon as the paper has been pressed they take it still warm to the drying
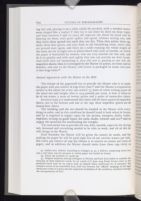
shaped like a capital T they lay it out sheet by sheet on those ropes,
and boys between 8 and 10 years old separate the sheets by hand and by
blowing on them, with great agility and speed, without tearing any, and
they leave them spread out until they are dry. Then they gather them up,
make them into quires, and take them to the burnishing room, where they
are pressed once again, and there on a table running the whole length of
the room are six to eight sites or places fitted with slabs of marble, on which
the paper is burnished by women, who are very suitable for this task, and
do it so quickly and with such agility that you can scarcely see their hands.
And while they are burnishing it, they also sort it, putting to one side the
imperfect sheets; then it is arranged by the Master in quires, in reams and in
bundles, and sent to the Owner, who leaves it packaged in reams and puts
it into large bales.[32]
Annual Agreement with the Master of the Mill
The Owner of the papermill has to provide the Master who is to make
the paper with 400 cantare of rags every year,[33]
and the Master is required to
return to the owner for every 100 cantare 75 bales of white writing paper of
the usual size and weight, that is 12½ pounds per ream. A bale is taken to
be of ten reams, a ream of twenty quires and a quire of twenty-five sheets.
In every ream it is understood that there will be three quires of imperfect
sheets, two at the bottom and one at the top; these imperfect quires are of
twenty-four sheets.
The building and the site should be handed to the Master with everything
in order, and in this condition he should hand it back when he leaves,
and he is required to supply ropes for the presses, stampers, shafts, boiler,
impidori, to keep in good repair the nails, shafts, reinette and seo,
[34]
and to
supply the materials for maintaining the troughs.
The said owner has to provide the size, felts, moulds, ropes for the drying
loft, firewood and everything needed to be able to work, and all of this he
will charge to the Master.
Each Saturday the Master will be given the money he needs, and for
making the paper he will be paid eight lire of our current money per bale.
For every 400 cantare of rags the Owner is to receive in return 300 bales of
paper, and in addition the Master should make from these rags thirty to
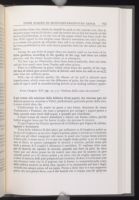
the price paper normally fetches, and the owner has to feel the benefit of this
increased production, as in the rest of the paper which has been made for
him. With regard to this surplus some Masters sometimes use little loyalty,
as a custom has grown up whereby they sell it to others, even though this
has been prohibited by law with heavy penalties both for the sellers and the
buyers.
Among the 300 bales of paper there are usually eight to ten bales of inferior
goodness, according to the quality of the rags, and these are called
gruzzotti, and the owner accepts them, as is customary.
The best rags are Florentine, then those from Lombardy, then our own,
and the least good come from Naples and other places.
There is a difference in price, which arises from the quality of the rags,
the best of which give several bales of fioretti, and these are sold at 20-25%
more than the ordinary price.
With rags of inferior quality the Master of the mill is allowed some
imperfections, which even out the difference of price, for the same consignment
of rags is used in manufacturing fioretti as in making ordinary paper.
Diligent enquiries among colleagues in Britain and Italy have failed to establish the
meaning of these italicized words. In an e-mail of 8 June 2004 Paolo Cevini refers to the
problems faced even by an expert such as himself when confronted by (I translate) `the
complex nature of an uncodified lexic, half way between the "official" language of the legal
documents (often in Latin) and the empirical vocabulary of the workforce, mediated through
the interpretation of Peri.'
Peri's text confuses here pile (= troughs) with stampers (= mazzi). I translate what
I take to be his meaning; and see note 18 below.
I use the equivalence 1 palmo = 25 cm in this translation; for exact measurements
of some surviving mill structures, which confirm the accuracy of Peri's figures, see Cevini,
pp. 187-188.
The standard length of the camshafts, which were usually made of beechwood, was
31 palmi, that is, about 7.75 m; see Cevini, p. 196 and note 22.
Once again Peri's text confuses the terms pile and mazzi, and again I translate what
I take to be his meaning. Subsequently he uses pile for troughs and mazzi for stampers,
without further confusion.
The type of large press described here is illustrated in a sixteenth-century ex voto
from Fabriano; two thick wooden screws, inserted into the bottom beam, one near each
end of the press, rise vertically to protrude through the upper beam, with the nuts above,
in the form of wooden collars with two horizontal handles, with which they can be screwed
down; see Calegari, La manifattura genovese della carta, Tavola II and p. 142.
The terms fioretto and fiorettone are found in other Italian paper-making areas,
though unfortunately not always with the same meaning; see Ezio Ornato et al., La carta
occidentale nel tardo medioevo (Rome: Istituto Centrale per la Patologia del Libro, 2001),
Tome I, pp. 335-355. They are also used to describe the quality of the finished product. In
this text fioretto is the top quality. In Genoa, brown-paper mills, which were smaller than
white-paper ones, usually with only one wheel, were called edifici da gruzzo.
According to Cevini, p. 190 and note 18, surviving examples are about 70 cm high,
1.3 m long and from 85 c to 1 m wide.
The cantara of the Italian text is a pre-decimalisation measure of weight, equalling
in Genoa 47.75 kg; see Cevini, p. 190, note 19.
The Italian pound (libbra, libra, lira) weighed about 300 g, considerably less than
the British and American pound (about 450 g).
In his earlier description of the mill Peri refers to only one vat, a detail borne
out by the surviving documentation, and also by the evidence of surviving structures.
In fact the hours worked in mid-seventeenth century Genoese paper mills, and so
the daily production of paper, were often greater than those given by Peri; see Calegari,
p. 108; Cevini, p. 205.
For confirmation of this substantial pause in the sizing during high summer see
Sabbatini, p. 58. Magagni's comments (pp. 52-53) are more nuanced: both hot weather and
really cold weather are unsuitable for making the size, but if it has to be made in summer,
it should be done during the night. The pause must have created serious problems, if only
of storage, in the Genoese white-paper mills.
Cevini records (p. 220) that even as late as the second half of the eighteenth century
paper was used instead of glass in the window openings of the mills, apart from those in the
drying lofts, with their shutters. The use of oil-paper instead of glass in the windows of an
inn near Venice is mentioned in an entry in Goethe's diary for 13 September 1786 (I owe
this reference to a note by Barry Watson in the British Association of Paper Historians
News, 56 [Autumn 2004], 7.)
![]() | Studies in bibliography | ![]() |