![]() | Studies in bibliography | ![]() |
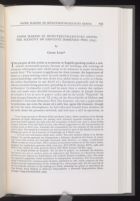
PAPER MAKING IN SEVENTEENTH-CENTURY GENOA:
THE ACCOUNT OF GIOVANNI DOMENICO PERI (1651)
by
Conor Fahy
[*]
THE purpose of this article is to present to English-speaking readers a substantial
seventeenth-century account of the buildings and workings of
a Genoese white-paper mill, which seems to be unknown to paper historians
outside Italy.[1]
The account is significant for three reasons: the importance of
Genoa as a paper-making centre in early modern Europe, the author's access
to local knowledge, and the date of the text, which makes it, as far as I know,
the earliest description in any detail of a European paper-mill and of the
relevant manufacturing processes, preceding by seventy-five years the account
in Chambers' Cyclopaedia (1728) and by more than a century the authoritative
and much more detailed treatments of the subject in Joseph Jérôme
de Lalande's L'art de faire le papier (1761) and in the article "Papeterie" by
Louis Jacques Goussier in vol. XI (1765) of the Encyclopédie of Diderot and
d'Alembert.[2]
Giovanni Domenico Peri, like Goussier, was not a paper-maker
by profession, nor even the owner of a mill, but, again like Goussier, though
not with the same thoroughness, he had informed himself from members of
the trade about the processes involved, and had seen a mill in operation, as
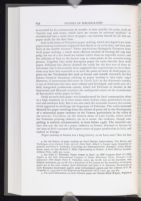
"merely rags and water, which have no viscous or resistant qualities," is
transformed into a stout sheet of paper—an emotion shared by all who see
paper made for the first time.
Italy is the home of European paper making, which developed from Arab
paper-making techniques imported into Spain at an early date, and then into
Italy in the twelfth century.[3]
Three innovations distinguish European from
Arab paper making: a much more efficient method of beating the rags into
pulp, the use of a size based on animal rather than on vegetable matter, and
the addition of lime to the beaten rags at some point in the manufacturing
process. Together they made European paper far more durable than Arab
paper. Fabriano has always claimed the credit for the first two of these innovations,
but it has recently been suggested that experiments in these directions
may have first occurred at or near the point of entry of Arab paper, i.e.
ports on the Tyrrhenian Sea such as Genoa and Amalfi. Certainly the first
known Genoese document relating to paper making is very early. 1235.[4]
However, if innovations did occur in North Italy in the thirteenth century,
it was at Fabriano that they were refined and developed, and made part of a
fully integrated production system, which led Fabriano to become in the
fourteenth and fifteenth centuries the undisputed centre of the manufacture
of fine-quality white paper in Italy.
From an early date paper was manufactured for local consumption, often
to a high standard, in or near many other Italian cities, particularly in central
and northern Italy. But it was not until the sixteenth century that serious
rivals appeared to challenge the hegemony of Fabriano. The vastly increased
demand for paper resulting from the advent of print led to the development
of a substantial paper industry in the Veneto, particularly in the valley of
the torrente Toscolano, on the western shore of Lake Garda, which served
the Venetian printing industry (or so it seems: the evidence, though compelling,
is entirely circumstantial, at least before 1548). The sixteenth century
also saw the rise of a paper industry in Genoa, destined to become by
the time of Peri's account the largest centre of paper production in Italy, and
indeed in Europe.
Paper making at Genoa has a long history, as we have seen.[5]
But the first
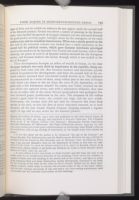
of the fifteenth century. Genoa was never a centre of printing in the Renaissance;
what fuelled the growth of its paper industry was the increased demand
for good-quality writing paper, brought about by the emergence of the early
modern state and its attendant bureaucracy. What was a steady growth in the
first half of the sixteenth century was turned into a rapid expansion in the
second half by political events, which gave Genoese merchants privileged
access to the markets of the Spanish New World and made Genoa, rather than
Antwerp, the point of arrival of Spanish bullion destined for the European
market, and Genoese bankers the means through which it was traded to the
rest of Europe.[6]
These developments brought an influx of wealth to Genoa. At the time
the paper industry was only third in importance in the republic, being surpassed
by both wool and silk. But Genoese bankers and merchants quickly
realized its potential for development, and from the second half of the sixteenth
century invested their new-found wealth heavily in it. The industry
was concentrated in a series of short, steep valleys just to the west of Genoa
itself, which run down to the sea from the crest of the Apennines, at this
point only a few kilometers inland.[7]
Its centre was Voltri, situated on the
coast where two separate rivers, one with a substantial tributary, flow into
the sea on either side of the town. Several geographical and geological features
favoured paper production in the area. The steepness of the valleys
created a good head of water, the rainfall was high, and the area windy.
Furthermore, the streams were fed not only by rainwater but from deep
springs in the rock, so that the flow of water remained constant, or at least
adequate, all the year round. Finally Genoese shipping ensured a regular
supply of rags and an easy outlet for the finished product.
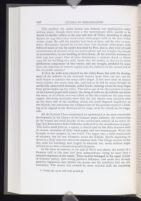
This product, for which Genoa was famous, was good-quality white
writing paper, though there were a few brown-paper mills, mainly to be
found in smaller valleys to the east and west of Voltri. According to official
figures, in 1544 there were twenty-nine white-paper mills in the three Voltri
valleys alone. By 1588 the number had risen to forty, and by 1612 to sixty-three.
Documents quoted by Cevini show that Genoese white-paper mills
followed more or less the model described by Peri, that is, they were all solid
constructions of masonry with two water-wheels and ten troughs, big enough
to accommodate, in one building of three floors, all the activities necessary to
turn rags into paper. One of these documents, a contract dated 12 March
1493 for the building of a mill, shows that the model, at least in its major
production component of two wheels and ten troughs, predated by many
years the injection of venture capital into the industry in the second half of
the sixteenth century.[8]
At first the mills were situated on the valley floors, but with the development
of the industry in the sixteenth century space there ran out, and the
mills began to colonize the steep valley slopes. A few were sited on natural
water-courses, but many were not, and had to be fed by water brought by
artificially constructed channels, called beudi, running across the steep slopes
from points higher up the valley. This led to one of the characteristic features
of the Genoese paper-mill scenery, the siting of mills on the hillside one below
the other, or in cascata, as it was called, so that they could use the same water
supply. Surviving structures show that the two wheels were normally sited
on the short side of the building, which was itself disposed lengthways on
the hillside, but sometimes the configuration of the ground required a building
to be aligned in the direction of the slope, with the wheels on the longer
side.
All the features I have mentioned are epitomized in the most remarkable
development in the history of the Genoese paper industry, the construction
in the second and third decades of the seventeenth century of an entire village,
San Bartolomeo delle Fabbriche, dedicated to the manufacture of paper.
This had a small palazzo, a square, a church and no less than nineteen mills
in cascata, seventeen of them white-paper and two brown-paper. Water was
brought to this complex by two beudi. The upper one, a solid construction
of masonry, ran for one kilometre across the hillside, finally depositing its
water in a little reservoir above the topmost mill. The village survives to this
day, with the buildings now largely in domestic use, many without major
alterations to their external structural features.
As the form of contract at the end of Peri's text shows, the master of a
Genoese mill at this time had little independence, being no more than a
salaried employee of the owner. These owners belonged to the upper reaches
of Genoese society, with strong political influence, and made sure through
punitive legislation that neither the master nor his workforce had any real
autonomy. The master was assisted by three salaried staff; the remaining
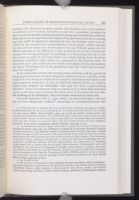
In addition to the vatman (lavorante in our text; sometimes, elsewhere in
Italy, lavorente) and the coucher (ponidore) this group included the studiente,
whose job it was to supervise every aspect of the processes involved in turning
rags into stuff.[9] It should be remembered that the Genoese mills were intended
for the manufacture of good-quality writing paper, which explains
the time and care taken over the beating of the rags. Without going into the
difficult question of the difference, if any, in this period in the manufacture
of paper for writing and paper for printing, it is interesting that one of the
few features of mills in the Lake Garda area which emerge from the documentation
available is their small size, compared to the Genoese mills. In
the period up to 1560, mills with two wheels rarely figure in these documents;
the typical Toscolano mill of the period had only one wheel and not more
than four troughs.[10]
In the eighteenth century the waning power of Genoa and the growth of
strong paper industries in other European countries led to a decline, made
terminal by the obstinate refusal of the majority of Genoese mill-owners and
paper-makers to modernize. As late as 1846 only eighteen of the 175 mills in
Liguria had adopted the Hollander, and only one had a paper-making
machine.[11]
These circumstances help to explain why so many mill structures
survive to this day, some in ruins, but others more or less intact because, like
the buildings of Le Fabbriche, they have been converted to other uses.
Giovanni Domenico Peri (c. 1590-1666) is an interesting figure who has
not yet been adequately studied.[12]
According to seventeenth-century biographical
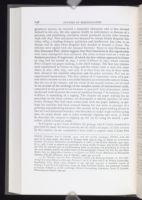
himself to the arts. He also appears briefly in mid-century as director of a
printing and publishing enterprise which produced sixteen titles between
1648 and 1650. This enterprise was financed by Anton Giulio Brignole Sale
(1605-1665), a leading Genoese politician and intellectual, but came to an
abrupt end in 1650 when Brignole Sale decided to become a Jesuit. The
editions were signed with the unusual formula: `Sotto la cura/direzione di
Gio. Domenico Peri', which suggests that Peri's functions in this organization
were more managerial than technical. His claim to fame rests on a work on
business practices, Il negotiante, of which the first volume appeared in Genoa
in 1639 and the second in 1647. I frutti d'Albaro of 1651, which contains
Peri's chapter on paper making, is the third volume. The first two volumes
were republished in Venice in 1649, and the whole work at least four times
there, in 1672, 1682, 1697, and 1707. It is clear from the text of these works
that, whatever his youthful education and his other activities, Peri was an
experienced businessman. The first volume of Il negotiante starts with general
advice on how to run a successful business in seventeenth-century Genoa,
but the rest of the volume, and the whole of the second volume, are devoted
to an account of the workings of the complex system of international credit,
controlled in this period by the Genoese at quarterly `fairs of payment', which
facilitated trade between the states of southern Europe.[13] In contrast, I frutti
d'Albaro is something of a ragbag. The chapter on paper making has no
precedent in the three volumes; no description is offered anywhere of other
trades. Perhaps Peri had some connections with the paper industry, or perhaps
his curiosity had been aroused during his two years as manager of a
printing and publishing business. His account of the paper-making process is
that of a well-informed outsider, who describes its major stages without going
into too much detail, and at times seemingly slipping into error, as when
he describes the vatman as topping up the vat by using his mould, a procedure
which is hard to credit.
In Chapter 14 of I frutti d'Albaro the passage which I have translated is
preceded by some rhetorical remarks on the utility of paper, of little interest
in this context. In my translation I have tried to express what I think Peri
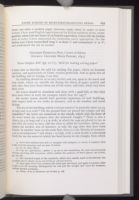
written. I have used English equivalents of the Italian technical terms, where
possible; when I do not know of an English equivalent, I have left the Italian
term in italics. I have annotated the translation where appropriate. For the
Italian text I have transcribed long `s' as short `s' and consonantal `u' as `v',
and modernised the use of accents.
Giovanni Domenico Peri, I frutti d'Albaro
(Genova: Giovanni Maria Farroni, 1651)
From Chapter XIV (pp. 63-71), "Mill for making writing paper"
I come now to describe the mill for making this paper, which on Genoese
territory, and particularly at Voltri, reaches perfection. And to speak first of
the building and its fittings, I say that
the building should be in an airy locality and site, open to the north and
west winds, which are suitable for drying the sheets of paper quickly and
well, after they have been taken out of the water, and later, when they have
been sized.
the waters should be abundant and clear, with a good fall, so that they
have more force to work the stampers which beat the rags.[14]
the master mason should have previous experience of such buildings,
with respect both to the works in masonry, and to the wooden and metal
fittings.
The site of the building, which is of two storeys,[15]
is normally about 23-25
m long and 10 m wide.[16]
On the ground floor are placed the troughs and the
camshafts;[17]
the latter are connected to the wheels, which with the force of
the water make the stampers beat the aforesaid troughs.[18]
There is also a
chest 3.75-4 m long and 2-2.5 m wide, in which the rags are placed to rot, so
that they are easier to beat, and the chest is called the mettidore. Other containers
are needed, also of masonry, to take the rags after they have been
beaten. In another room on the same floor there is a vat, likewise of masonry,
5 m in circumference[19]
and about 1 m high, with a chest beside it containing
ready for use the material which has been beaten in the troughs, from which
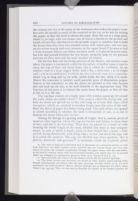
with the mould as much of the material to the vat, as he uses in making
the paper, so that the level is always the same. Near the vat is a large press,
about 2.5 m high, with two beams, one of which is buried in the ground and
stands on two feet, also buried in the ground, to give it stability; and to hold
the beams firm they have two wooden screws with metal pins, and two nuts
on the screws to grip and exert pressure on the upper beam.[20] As soon as half
a ream of paper, that is, 250 sheets, has been made, it is placed between woollen
felts and pressed between the two beams, using the nuts, by the physical
exertion of three men and the same number of women.
On the first floor are the living quarters of the Master, and another room
where the paper is burnished, called the lisciadore. A further room is used to
clean the rags of dust and shred them; this is called the crolladore. In yet
another room is a large copper boiler with a fire, a little over 1 m in height
and 2.5 m in circumference, in which the size is heated; near it is a container
about 1.25 m long and 75 cm wide, which holds the size, when it is made.
Above this container is another small portable press of dimensions proportionate
to the container; in this the sheets are pressed so that they become
soft and soak up the size, as we shall describe at the appropriate time. The
function of this press is to remove the water from the paper, so that all that
is left in it is the size.
The top floor consists of a single room with window openings all around
the walls, which are called rebatte.
[21]
The room is called the drying loft, and
here the sheets are spread out to dry and hung on certain thin ropes called
terragnine, which are attached to wooden frames near the eaves of the roof.
Here the sheets of paper dry before being sized. The said rebatte are opened
or closed according to whether the wind is favourable or not, so as not to
damage the sheets when they are wet.
Among the fittings is a grating made of trappe, that is, narrow pieces of
wood set close together, where the rags are beaten and shaken to clean them
of dust, and this is the first stage. Then they are placed on a bench or table
running the whole length of the room, divided into three or four compartments,
in each of which is fixed a piece of iron shaped like a hand, a little
curved, facing downwards, with sharp edges, to tear and shred the rags, and
it is called the squarcio. The rags are divided into three qualities, that is
fioretto, fiorettone and gruzzoto.
[22]
A workman called the studiente places
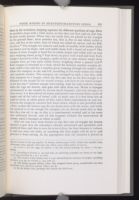
he sprinkles them with a little water, so that they can heat and rot and thus
be more easily beaten. When they are ready they are placed in the troughs
on the ground floor; these number ten, that is, five to one wheel, called a
cinci, and five to the other, four of which are called da repisto, and the fifth
da sfilato. [23]
The troughs are concave and made of marble, with insides which
are almost oval in shape, and each holds about half a barrel of water.[24] The
bottom of these troughs is lined for its whole length and width with an iron
sheet weighing about 50 kg,[25] kept firmly in place with wood and lead. Each
trough is beaten by three stampers, made of oak or some similar wood; these
stampers have 30 iron nails called biette, weighing about a pound each.[26]
Each stamper is attached to a shaft, which fits between another wooden element
called a key and has a wooden pivot running through the middle; this
allows the stampers to rise and fall, according as the water makes the wheel
and camshaft revolve. The stampers are arranged in such a way that, with
three stampers to a trough, when the first one rises in the first trough, it is
followed by the second in the second trough, and then by the third stamper
in the last one,[27] without anyone intervening. And the said studiente knows
when the rags are beaten, and goes and takes them out. Water is brought
continuously to the troughs by certain small channels, and even though it is
clean water, it is first placed in basins and passed over certain filters made of
copper and of the hairs of horses' tails, to make sure it is free from bits of
wood or straw, or other pieces of dirt, and it flows continuously in and out.
It leaves the trough by another hole lower down, which is also provided with
a filter, so that the beaten rags do not drain away with the water; and while
the material is in the trough the stampers are so cleverly made that as they
beat they also stir it up, so that it is continuously washed and at the same
time uniformly beaten; and all this happens without the intervention of
anyone, until it becomes as white as milk.
After the rags have been beaten in this first row of troughs the beaten
material is put into the containers already mentioned and sprinkled with
powdered lime, and thus it stays for several days; the lime foments it, reduces
it, and eats away the hairs, or anything else that might still be in it, and
prevents it from rotting. At the appropriate time the material is placed in
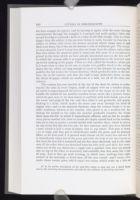
continuously through the troughs, it is purged and made perfect. After this
second beating it is placed a little at a time in the fifth trough. This is a little
bigger than the others; it has no iron lining or nails, because its function is
simply to dilute with water the beaten material which comes into it and
then stays there, but it has on the bottom a slab of millstone grit. The stampers
have no nails, but it is true that they are larger than the others, and as they
beat they dilute the material until it seems just like snow. It is straightaway
placed in the chest which we have already mentioned next to the first vat,[28]
to which the vatman adds it as required, in proportion to the material used
up in the making of the paper. There is a boy called the lavadore, whose job
it is from time to time to stir one or maybe two paddles fixed to the ceiling
above the vat, which are long enough to reach to the bottom; by moving the
paddles the boy makes the beaten material, which gradually sinks to the bottom,
rise to the surface; and thus the stuff is kept uniformly dense, so that
the sheets of paper, which are made one at a time, are all of the same consistency.
The vatman has two moulds of the size of the sheet he wishes to make,
exactly the same in every respect, made of copper wire on a wooden frame,
on which is superimposed the device and name of the owner of the mill. To
handle the mould he has another wooden frame, made like a picture frame,
which he puts over it; he then lowers it carefully with both hands, puts it in
the water and pulp of the vat, and then takes it out gradually and gently,
shaking it a little, which makes the water run away through the mesh of
copper wire, and so the material thickens; then the vatman hands it to another
workman, known as the coucher, who places it on a woollen felt. Inclining
the mould to the right the coucher gradually transfers the whole
sheet onto the felt, to which it immediately adheres, and on this he straightaway
places another felt; then he hands the empty mould back to the vatman,
who gives him in return a second mould with another sheet, which he places
on top of the felt like the first one. So they continue until they have finished
a post, which is half a ream of paper, that is, 250 sheets. This post is about
1.12 m high, and they put it immediately under the press, and by physical
effort, as we have said, it is pressed until almost all the water has run out. It
is immediately taken out of the press and with the help of the boy known as
the layer the first felt is removed and the first sheet detached, and in the same
way all the other sheets are detached from the felts with such skill, that sometimes
out of the 250 sheets not a single one is spoiled; then they are placed
one on top of the other so accurately and carefully that they seem like a bar
of soap. And so they go until evening, in which time, working from eight
o'clock in the morning—a fixed time, all the year round—until sunset, they
make about twenty posts, which equal ten reams, which make up a bale of
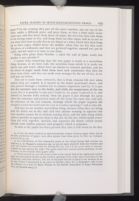
other, under a different press, and press them, so that a little more water
comes out, and they leave them there all night; the next day they take them
to the drying room to dry, and hang them on thin ropes; and so as not to
tear them they have to take five or six sheets at a time, which they then hang
up on these ropes, folded down the middle; when they are dry they seem
like pieces of cardboard, and they are gathered together, opened out, put in
a pile, and left until it is time to size them.
Sizing takes place from October 1 until the end of June; really hot
weather is not suitable.[30]
I cannot help remarking that the way paper is made is a marvellous
thing, because, as we have said, the materials from which it is made are
merely rags and water, which have no viscous or resistent qualities, and yet
the sheets of paper made from them have such consistency that they are
better than cloth, and they are made even stronger by the use of size, as we
shall now say below.
This size is made from carnuccio, that is from remains left over when
animal skins are tanned. It is heated in the boiler mentioned above, and
then poured through a woollen felt to remove impurities and fat. It is put
into the container next to the boiler, and while the temperature of the size
is such that it is possible to put one's hand in, the paper is placed in it, and
allowed to become fully soaked; then the paper is put through the press
above the container and pressed until all the water has come out, and only
the substance of the size remains, through which the paper acquires the
strength to resist the wind and the rain in window-openings,[31]
and to take ink.
And here we see another marvellous thing, because when they are being
sized the sheets are so dry and arid that anyone wanting to separate one
from another cannot do so without tearing them, and the only thing which
makes it possible to separate them is the size. So the size, which makes everything
else stick together, unsticks and separates the sheets—which occurs
through some hidden potency and property which it possesses.
As soon as the paper has been pressed they take it still warm to the drying
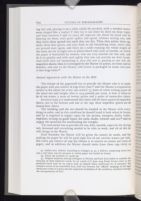
shaped like a capital T they lay it out sheet by sheet on those ropes,
and boys between 8 and 10 years old separate the sheets by hand and by
blowing on them, with great agility and speed, without tearing any, and
they leave them spread out until they are dry. Then they gather them up,
make them into quires, and take them to the burnishing room, where they
are pressed once again, and there on a table running the whole length of
the room are six to eight sites or places fitted with slabs of marble, on which
the paper is burnished by women, who are very suitable for this task, and
do it so quickly and with such agility that you can scarcely see their hands.
And while they are burnishing it, they also sort it, putting to one side the
imperfect sheets; then it is arranged by the Master in quires, in reams and in
bundles, and sent to the Owner, who leaves it packaged in reams and puts
it into large bales.[32]
Annual Agreement with the Master of the Mill
The Owner of the papermill has to provide the Master who is to make
the paper with 400 cantare of rags every year,[33]
and the Master is required to
return to the owner for every 100 cantare 75 bales of white writing paper of
the usual size and weight, that is 12½ pounds per ream. A bale is taken to
be of ten reams, a ream of twenty quires and a quire of twenty-five sheets.
In every ream it is understood that there will be three quires of imperfect
sheets, two at the bottom and one at the top; these imperfect quires are of
twenty-four sheets.
The building and the site should be handed to the Master with everything
in order, and in this condition he should hand it back when he leaves,
and he is required to supply ropes for the presses, stampers, shafts, boiler,
impidori, to keep in good repair the nails, shafts, reinette and seo,
[34]
and to
supply the materials for maintaining the troughs.
The said owner has to provide the size, felts, moulds, ropes for the drying
loft, firewood and everything needed to be able to work, and all of this he
will charge to the Master.
Each Saturday the Master will be given the money he needs, and for
making the paper he will be paid eight lire of our current money per bale.
For every 400 cantare of rags the Owner is to receive in return 300 bales of
paper, and in addition the Master should make from these rags thirty to
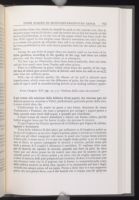
the price paper normally fetches, and the owner has to feel the benefit of this
increased production, as in the rest of the paper which has been made for
him. With regard to this surplus some Masters sometimes use little loyalty,
as a custom has grown up whereby they sell it to others, even though this
has been prohibited by law with heavy penalties both for the sellers and the
buyers.
Among the 300 bales of paper there are usually eight to ten bales of inferior
goodness, according to the quality of the rags, and these are called
gruzzotti, and the owner accepts them, as is customary.
The best rags are Florentine, then those from Lombardy, then our own,
and the least good come from Naples and other places.
There is a difference in price, which arises from the quality of the rags,
the best of which give several bales of fioretti, and these are sold at 20-25%
more than the ordinary price.
With rags of inferior quality the Master of the mill is allowed some
imperfections, which even out the difference of price, for the same consignment
of rags is used in manufacturing fioretti as in making ordinary paper.
Diligent enquiries among colleagues in Britain and Italy have failed to establish the
meaning of these italicized words. In an e-mail of 8 June 2004 Paolo Cevini refers to the
problems faced even by an expert such as himself when confronted by (I translate) `the
complex nature of an uncodified lexic, half way between the "official" language of the legal
documents (often in Latin) and the empirical vocabulary of the workforce, mediated through
the interpretation of Peri.'
Peri's text confuses here pile (= troughs) with stampers (= mazzi). I translate what
I take to be his meaning; and see note 18 below.
I use the equivalence 1 palmo = 25 cm in this translation; for exact measurements
of some surviving mill structures, which confirm the accuracy of Peri's figures, see Cevini,
pp. 187-188.
The standard length of the camshafts, which were usually made of beechwood, was
31 palmi, that is, about 7.75 m; see Cevini, p. 196 and note 22.
Once again Peri's text confuses the terms pile and mazzi, and again I translate what
I take to be his meaning. Subsequently he uses pile for troughs and mazzi for stampers,
without further confusion.
The type of large press described here is illustrated in a sixteenth-century ex voto
from Fabriano; two thick wooden screws, inserted into the bottom beam, one near each
end of the press, rise vertically to protrude through the upper beam, with the nuts above,
in the form of wooden collars with two horizontal handles, with which they can be screwed
down; see Calegari, La manifattura genovese della carta, Tavola II and p. 142.
The terms fioretto and fiorettone are found in other Italian paper-making areas,
though unfortunately not always with the same meaning; see Ezio Ornato et al., La carta
occidentale nel tardo medioevo (Rome: Istituto Centrale per la Patologia del Libro, 2001),
Tome I, pp. 335-355. They are also used to describe the quality of the finished product. In
this text fioretto is the top quality. In Genoa, brown-paper mills, which were smaller than
white-paper ones, usually with only one wheel, were called edifici da gruzzo.
According to Cevini, p. 190 and note 18, surviving examples are about 70 cm high,
1.3 m long and from 85 c to 1 m wide.
The cantara of the Italian text is a pre-decimalisation measure of weight, equalling
in Genoa 47.75 kg; see Cevini, p. 190, note 19.
The Italian pound (libbra, libra, lira) weighed about 300 g, considerably less than
the British and American pound (about 450 g).
In his earlier description of the mill Peri refers to only one vat, a detail borne
out by the surviving documentation, and also by the evidence of surviving structures.
In fact the hours worked in mid-seventeenth century Genoese paper mills, and so
the daily production of paper, were often greater than those given by Peri; see Calegari,
p. 108; Cevini, p. 205.
For confirmation of this substantial pause in the sizing during high summer see
Sabbatini, p. 58. Magagni's comments (pp. 52-53) are more nuanced: both hot weather and
really cold weather are unsuitable for making the size, but if it has to be made in summer,
it should be done during the night. The pause must have created serious problems, if only
of storage, in the Genoese white-paper mills.
Cevini records (p. 220) that even as late as the second half of the eighteenth century
paper was used instead of glass in the window openings of the mills, apart from those in the
drying lofts, with their shutters. The use of oil-paper instead of glass in the windows of an
inn near Venice is mentioned in an entry in Goethe's diary for 13 September 1786 (I owe
this reference to a note by Barry Watson in the British Association of Paper Historians
News, 56 [Autumn 2004], 7.)
Italian text: balloni. According to Calegari, p. 57, a ballone, comprising about two
and a half bales, was the measure in which paper was traded in Genoa.
From Chapter XIV (pp. 63-71), "Fabrica della carta da scrivere"
E per venire alla relatione della fabbrica d'essi paperi, che riescono qua nel
dominio genovese, massime a Voltri, perfettissimi, parlando prima della casa,
& arnesi stabili dico, che
L'habitatione ha da essere in paese e sito fresco, dominato da vento
Tramontana e Ponente, che sono a proposito per asciugar i paperi presto e
bene, quando sono tratti dall'acqua, e quando poi s'incollano.
L'acque hanno da esservi abondanti e chiare, con buona caduta, perché
habbia maggior forza per far batter le pile, che pestano le straccie.
Il capo d'opera ha d'haver sperienza di tal fabbrica per l'opera di calcina,
legnami e ferramenti.
Il sito della fabbrica di doi solari, per ordinario va di longhezza palmi 90
in 100 e di larghezza 40 in circa. Sopra il primo piano a terreno se vi mettono
le pile con gli alberi congionti alle ruote, le quali con l'acqua fanno pistare
le dette pile, o siano mazzi. Ci va poi un troglio longo palmi 15 in 16 e largo
otto in diece, in questo ripongonsi le straccie a marcire, perché siano più
facili a pistare, & il troglio è chiamato il mettidore. Vi vogliono altre casse
pur di materia da riponer le straccie, quando son fatte in pisti. In altra
stanza pur nel detto piano ha da esservi una tina pur di materia in giro
rotondo palmi 20 e di altezza palmi 4 in circa, con un troglio appresso, ove
si tiene la materia delli pisti preparati per lavorare, di dove il Lavorante (che
così chiamasi colui che fa il papero) con la forma va somministrando tanta
della sudetta materia in detta tina, quanta si va sminuendo nel fare i fogli,
accioché stia sempre piena ad un segno. Presso a detta tina vi è una soppressa
grossa, che sarà palmi diece, con li doi banchi che vi vanno, uno de' quali sta
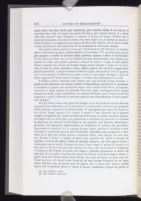
mettono due vide di legno con perni di ferro, per tenerli stretti, & a dette
vide due morse[35] per stringere e calcare il banco di sopra. Subito che è
formato il papero, cioè mezza risma, che sono fogli 250, si ripone in mezzo a'
feltri di lana, e si suppressa nel mezzo di detti doi banchi con le dette morle
a forza di braccio col ministerio di tre huomini & altretante donne.
Nel primo solaro sono le stanze per l'habitatione del Maestro, & un'altra
dove si lisciano li paperi, addimandato il Lisciadore. V'è un altro sito ancora
per purgar e crollar le straccie dalla polvere; questo è detto il Crolladore.
Ve n'è anco un altro, ove sta la Caldaia di rame assai grande, con fogone, per
cuocer la colla, alta palmi quattro e mezzo in circa, e larga in giro palmi
diece; a questa sta vicino un troglio longo palmi cinque e largo tre in circa,
ove si tiene la colla, quando è cotta. Sopra questo sta un'altra soppressetta
piccola portabile, e proportionata al detto troglio, nel quale si calca il papere,
e se vi fa amollire & imbeverare, come si dirà a suo luogo. Bisogna a forza di
detta soppressa[36]
farne uscire l'acqua, e vi resta sola incorporata la colla.
L'ultimo solaro contiene una stanza sola con balconi d'ogn intorno, a'
quali si dice Rebatte. La stanza è detta lo Spanditore, perché se vi spandono
e stendono li paperi per asciugarli sopra certe cordicciuole dette terragnine,
attaccate a' legni presso alla gronda del tetto. Qui s'asciugano detti paperi
formati in fogli, e poi s'incollano. Le sudette Rebatte con li venti favorevoli
s'aprono, e con li contrarij si serrano, perché non dannifichino li detti paperi
così bagnati.
Fra gli arnesi sono una grata di trappe, o sia di tavolette strette discoste
un poco l'una dall'altra, ove si sbattono e crollano dette straccie per purgarle
dalla polvere, e questa è la prima mano. Si ripongono poi sopra un banco, o
sia tavola, longa quanto è la stanza, a quale vi son ripartiti tre o quattro
luoghi, ad ogn'uno de' quali sta fisso un ferro come la mano, un poco adunco,
col taglio che sta all'in giù, per squarciare e stritolare le straccie, e si chiama
lo Squarcio. Le straccie si dividono in tre qualità, cioè fioretto, fiorettone e
gruzzoto. Un operario addimandato lo Studiente le colloca nel mettidore,
ripartendo le qualità; ivi le asperge di poc'acqua, perché si scaldino e marcischino,
e si possino pistare più facilmente. Quando sono preparate si mettono
in le pile nel primo piano a numero diece, cioè cinque ad una rota,
che dicono a Cinci, e cinque all'altra rota, quattro de' quali si dicono da
repisto, e l'altra da sfilato. Sono di marmo concave, col vaso quasi ovato, e
teniranno mezzo bacile d'acqua in circa l'una; sopra il piano di queste vi è
una piastra di ferro di peso un cantaro in circa, che tiene tutta la longhezza
e larghezza del fondo, al quale con legno e piombo benissimo si unisce. In
ogn'una di esse pile vi batton tre mazzi di rovere o di altro legno simile, a'
quali sono fissi trenta denti detti biette, che sono di ferro, in peso una lira
l'uno in circa, e li mazzi sono attaccati ad una stanga fraposta ad un legno
detto Chiave, con un perno pur di legno, che vi passa per mezzo; questo
opera che si possino alzare e calare li mazzi, conforme l'acqua fa girare la
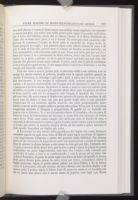
tre mazzi per pila, alzandosi uno nella prima pila, segue il secondo nell'altra,
così il terzo nell'ultima, senza che vi assista alcuno; & il detto Studiente sa
l'hora che devono esser pisti, e va a levarli. Vi sono poi certi canaletti, che
portano di continuo l'acqua in dette pile; & ancorché sia acqua netta, la
fanno purgare in trogli, e poi passare sopra certe telette tessute di rame e di
peli di coda di Cavallo, perché non vi restino né busche, o sian festuche, né
altre immonditie, e di continuo entra & esce. Passa poi nella pila per un'altro
buco più basso, e vi è parimente la detta teletta, acciò che con l'acqua non
vadino via li pisti, e mentre sta in la pila li mazzi son fatti con tale arte, che
secondo che pistano fanno anco voltare il pisto, acciò che si lavi di continuo,
e che resti pisto ugualmente, il che segue senza l'assistenza d'alcuno, a tal che
restano poi bianche come latte.
Pisti che sono a queste prime pile, si mettono nelle casse sudette, e se vi
sparge fra mezzo calcina in polvere, stando così in riposo qualche giorni; la
calcina li fomenta, li ristringe e gli rode i peli, o altro che vi fusse, e fa che
non marciscono. A suo tempo si collocano nelle sudette quattro pile da
repisto, e di nuovo repistandole con l'acqua che di continuo vi entra & esce,
si purgano e perfettionano. Repistato si mette a poco la volta in sudetta pila
da sfilato, la quale è un poco più grande della altre; non ha piastra né denti
di ferro, perché solo ha da stemprare con l'acqua la materia che v'entra e
più non esce. Ha però sopra il fondo una piastra di pietra da molino, & alli
mazzi non ha denti; è vero che son più grossi degli altri, e così pistando
stemperano di tal maniera quella materia che pare propriamente neve.
Subito si mette nello troglio sudetto presso alla prima Tina, ove il Lavorante
n'aggiunge secondo il bisogno a proportione di quelle ne va levando nel
papero che si fabbrica. Vi è un Garzonetto detto il Lavadore, che ha cura di
tanto in tanto di rimescolare un bastone, o siano doi, che attaccati al solaro
sopra detta Tina sono tanto longhi che arrivano sino al fondo di essa, e
menando li detti bastoni fa venire a galla li pisti, quali a poco a poco scendono
al fondo, per tenire la materia sempre densa ad un modo e poter formare li
fogli uguali, facendosi un foglio per volta.
Il Lavorante ha doe forme della grandezza del foglio che vuole formare,
amendue uguali in ogni cosa, fatte di filo di rame sopra un telaro di legnetti,
a cui improntano l'impresa e nome del patrone della fabbrica. Per maneggiarla
ha un telaro pur di legno fatto come una guarnitione a modo di quadro,
dove fa entrare la detta forma; a doi mani la cala giù per filo, l'infonde nell'acqua
e materia della detta tina, poi la tira a poco a poco di piano in piano
crollandola un poco leggiermente, con fare che l'acqua vada colando per
quelle file di rame, e così si va condensando; e così lo porge ad un'altro, che
si dice il Ponidore, il quale lo pone sopra un feltro di lana; piegando la forma
dalla parte destra pian piano la calca tutta sul feltro, restandovi subito il
foglio attaccato, sopra il quale mette subito un altro feltro, e dà la forma
vuota al Lavorante, che gli ritorna un'altra forma con un'altro foglio, e lo
ripone come il primo sopra il feltro. Così di mano in mano si va facendo, sin
che sia finita una posta, che è mezza risma di papero, cioè fogli 250. Resta
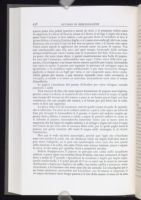
la soppressa, & a forza di braccia (come si è detto) si stringe a segno che n'esce
quasi tutta l'acqua; si leva subito, e col garzone detto il Levadore si leva il
primo feltro e si stacca il primo foglio, e si vanno staccando gli altri con tanta
destrezza, che in tutti li 250 tal hor non ne guasta uno, e li ripone uno sopra
l'altro tanto uguali & aggiustati che restano come un pane di sapone. Van
così continuando sino alla sera, nel qual tempo, lavorando dalle ott'hore
(tempo stabilito per tutto l'anno) sino al tramontar del Sole, fabricano circa
20 poste, che sono risme diece, e queste constituiscono una balla di papero.
La sera poi l'uniscono, collocandolo uno sopra l'altro sotto differente soppressa,
e lo stringono, e ne fanno uscire ancora qualche poc'acqua, lasciandolo
così tutta la notte; il giorno poi seguente lo portano ad asciugare sopra lo
spanditore, e lo stendono sopra cordicciuole; e per non stracciarlo bisogna
pigliarlo a cinque in sei fogli per volta, e così s'appende sopra dette cordicciuole
giusto per mezzo, a poi asciutto restando come tanti cartonetti, si
raccoglie, si stende e si mette in mucchio, lasciandovisi stare sino al tempo
d'incollarlo.
Li paperi s'incollano dal primo d'Ottobre per tutto Giugno, essendo
contrarii i caldi.
Non lasciarò di dire che resta questa formatione di papero maravigliosa,
perché, come si è detto, la materia di che si fa è solo straccie & acqua, le quali
non hanno del viscoso né del tenace, e pure se ne fanno questi fogli così ben
condensati che son meglio che tessuti, e si fanno poi più forti con la colla,
come si dirà qui appresso.
La detta colla si fa di carnuccio, cioè di quelli avanzi di pelle di animali,
che si affaitano. Va cotta in la caldara sudetta, e poi si cala sopra un feltro di
lana per levargli le immonditie & il grasso; si mette nel sudetto troglio appresso
detta caldara, e mentre è calda a segno di poterli soffrire le mani, se
vi infonde il papero, lasciandovelo imbeverar bene; poi si mette sotto la
soppressa che sta sopra lo troglio sudetto, e si stringe a segno che tutta l'acqua
esce fuora; ne gli resta solo la sostanza della colla, per la quale piglia forza il
papero, per poter resistere alli venti & acqua nelle stamegne, & al ricever
l'inchiostro.
Hor qui si vede un'altra maraviglia, perché que' fogli che s'incollano
sono così asciutti & aridi, che chi distaccar vuole un foglio dall'altro non si
può senza romperlo, né si può con qualsivoglia altra cosa che con questa
colla staccare; e la colla, che tutte l'altre cose attacca insieme, stacca e separa
la carta, il che segue per qualche virtù e proprietà occulta.
Subito disoppressato il papero lo portano così caldo nello spanditore
sudetto, e posto sopra un tavolino detto Predola, con uno stromento di legno
fatto a modo di T grande i Spanditori lo stendono a foglio per foglio sopra
quelle cordicciuole, e li putti piccoli di 8 in 10 anni con le mani lo staccano
similmente a foglio per foglio e col soffio, con molta agilità e prestezza, senza
stracciarne, e lo lasciano così steso sino che sia asciutto. Lo raccolgono poi e
ne fanno quinterni, portandoli nel Lisciadore, ove di nuovo si soppressa, &
ivi sopra un banco tanto longo quanto è il sito della stanza vi sono sei in otto
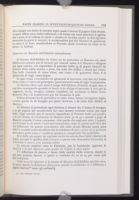
al quale uffitio sono molto addattate, e lo fanno con tanta prestezza & agilità,
che a pena se le vedono le mani; e mentre lo lisciano ancora lo distinguono,
mettendo da parte li mezetti; & accommodato poi dal Maestro in quinterni,
in risme & in fasci, mandandolo al Patrone, quale involtato in risme lo fa
metter in balloni.
Concerto col Maestro dell'Edifitio annualmente
Il Patrone dell'Edifitio da Carta ha da provedere al Maestro che deve
fabbricarla cantara 400 di straccie per ciascun' anno, & il Maestro è obligato
per ogni cantara 100 rispondere al patrone balle 75 di paperi bianchi da
scrivere della solita misura e peso, che sono lire dodici e mezza per risma.
Una balla s'intende di risme diece, una risma è di quinterni venti, & il
quinterno di fogli venticinque.
In ogni risma s'intendono tre quinterni di mezzetto, cioè due nel fondo
d'essa risma e l'altro sul principio; questi mezzetti sono di fogli ventiquattro.
Al Maestro deve esser dato il luogo dell'Edifitio all'ordine d'ogni cosa, e
così deve consignarlo quando lo lascia, & ha obligo di proveder li cavi per le
suppresse, masse, stanghe, caldare, impidori, far acconciar le Biete, Leve,
Reinette, Seo e le manifatture per far acconciar le pile.
Il detto Patrone ha da provedere la colla, feltri, forme, terragnina, legne,
e tutto quello fa di bisogno per poter lavorare, e di tutto darà debito al
Maestro.
Al Maestro si provedono ogni Sabbato li danari che li fanno di bisogno,
e se gli pagano per manifattura lire otto moneta corrente nostra per ogni
balla. Ogni cantare 400 di straccie rispondono al Patrone balle 300 paperi,
e di più danno di crescimento al Maestro balle 30 in 40 e questo si paga al
Maestro secondo il corso commune, cioè quello che sogliono valer li paperi,
& il Patrone ha da sentir l'utile nel crescimento, come lo sentirà nell'altro per
lui fabbricato. In questo crescimento alle volte alcuni Maestri usano poca
fedaltà, essendo stato introdotto che lo vendono ad altri, se ben ciò la giustitia
sotto gravi pene tanto a' venditori quanto a' compratori l'ha prohibito.
In le balle 300 paperi ne sogliono uscire da otto in diece balle inferiori di
bontà, secondo le qualità delle straccie, e questi sono domandati Gruzzotti, &
il Patrone li riceve, così essendo solito.
Le straccie migliori sono le Firentine, poi le Lombarde, appresso le
nostrali, e le più inferiori sono quelle di Napoli & altre parti.
V'è differenza di prezzo, e nasce dalle qualità della straccia, dando le
più fine qualche fioretti, e questi si vendono da 20 in 25 per cento più
dell'ordinario.
Nelle straccie inferiori si fa buono al Maestro dell'Edifitio qualche tara,
la quale uguala la differenza del prezzo, poiché la medesima va a fabbricar i
paperi fioretti,[37]
come gli ordinarij.
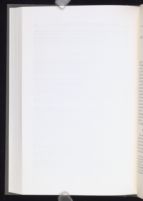
I am deeply grateful to Richard Hills and Brian Luker, fellow members of the British
Association of Paper Historians, for making their technical expertise available to me, to
Laura and Giulio Lepschy for help with the translation of Peri's text, and to Anna Giulia
Cavagna, Fiorenzo Toso and Paolo Cevini, who offered suggestions on the interpretation of
technical terms in Peri's text. Naturally the responsibility for the contents of this article is
entirely mine. The material it contains was first presented as part of the Sandars Lecture in
Bibliography given at the University of Cambridge on 6 March 2002.
And not very well known inside Italy, either. The only modern edition is in Manlio
Calegari, `La cartiera genovese tra Cinquecento e Seicento', Quaderni del Centro di studio
sulla storia della tecnica del Consiglio Nazionale delle Ricerche, 12 (1984), a publication
difficult to come by even in Italy. Peri's account is extensively drawn on in two recent books,
Calegari's La manifattura genovese della carta (sec. XVI-XVIII) (Genoa: ECIG, 1986) and
Paolo Cevini, Edifici da carta genovesi (Secoli XVI-XIX) (Genoa: SAGEP, 1995).
See Joseph Jérôme de Lalande, `Art de faire le papier', in Académie des Sciences,
Descriptions des arts et métiers, faites ou approuvées par Messieurs de l'Académie Royale
des Sciences Avec Figures en Taille-Douce, vol. I (Paris: Desaint & Saillant, 1761). The work
was separately paginated, which facilitated its independent circulation. The Encyclopèdie
article is illustrated by a famous series of plates, published in 1767, which comprise the first
detailed pictorial representation of the workings of a white-paper mill. All the material in
the Encyclopédie relevant to the making of a book, including the plates, is reproduced in
Giles Barber, Book Making in Diderot's Encyclopédie: a Facsimile Reproduction
(Farnborough:
Gregg International, 1973).
For the history of paper making see Dard Hunter, Papermaking: The History and
Technique of an Ancient Craft, 2nd ed. (New York: Alfred A. Knopf, 1947), frequently reprinted;
and Peter F. Tschudin, Grundzüge der Papiergeschichte (Stuttgart: Anton Hiersemann,
2002); see also Richard L. Hills, Papermaking in Britain: A Short History (London:
Athlone Press, 1988), pp. 13-29.
See Peter F. Tschudin, `Paper Comes to Italy', in IPH Congress Book 12 (1998):
Papers of the 24th International Congress of Paper Historians, Porto, Portugal, 11-20
September 1998 (Basel: Peter F. Tschudin, 2001), pp. 60-66; text of the document, with
English translation, pp. 65-66. For a discussion of the reasons for the durability of European
paper see, in the same volume, Jozef Dabrowski and John S. G. Simmons, `Permanence of
early European hand-made papers: some technological aspects and the evidence of F. M.
Grapaldo (c. 1494) and of the Regensburg Regulations (XVI 2/2c)', pp. 253-263.
For more information on early Genoese paper see Charles Moïsé Briquet, `Papiers et
filigranes des archives de Gênes, 1154 à 1700', first published in Atti della Società Ligure di
Storia Patria, 19 (1887), pp. 269-394, and reprinted in Briquet's Opuscula: The Complete
Works of Dr. C. M. Briquet without "Les filigranes", Monumenta Chartae Papyraceae
Historiam Illustrantia, IV (Hilversum: The Paper Publications Society, 1955) pp. 171-218.
This article contains one of the great understatements of scholarship, when Briquet refers to
his contribution, with its 594 tracings of watermarks, as "de simples notes d'un touriste en
passage".
It was this which led the period to be christened "the age of the Genoese"; see
Fernand Braudel, The Mediterranean and the Mediterranean World in the Age of Philip II,
translated from the French by Siân Reynolds, 2nd ed. (Berkeley: Univ. of California Press,
1995), I, pp. 500-508. Braudel's views on the importance of Genoa at this time are summarized
in the article `Le siècle des Génois s'achève-t-il en 1627?', in Braudel, Autour de la
Méditerranée, édition établie et presentée par Roselyne de Ayala et Paule Braudel (Paris:
Éditions de Fallois, 1996), pp. 433-446.
In what follows I draw extensively on Paolo Cevini's splendid book (see note 1), an
erudite study by an architectural historian of the buildings which served the industry, a
number of which were still standing in the second half of last century, and figure in many
of the numerous black and white illustrations, mainly photographs, contained in the book.
For the workings of the mills Cevini relies on Peri's account, fleshed out by much documentary
evidence, which helps to recreate the feverish tempo of life in the paper valleys,
with the daily comings and goings of rags and paper, the never-ending maintenance work
on the mills, and the continual construction of new buildings.
In Villa Basilica in Tuscany the term used for this workman was reggente di pila;
see Renzo Sabbatini, Di bianco lin candida prole: la manifattura della carta in età moderna
e il caso toscano (Milan: FrancoAngeli, 1990), pp. 57-58. In another Tuscan source, the
interesting if sentimental memoirs of a twentieth-century mill-owner from Pescia, it is the
maestro (called ministro in this area) who is responsible for the preparation and treatment
of the rags; the studente is concerned solely with the beating process; see Carlo Magnani,
Ricordanze di un cartaio (Alpignano, Alberto Tallone, 1979), pp. 22-34.
152 documents relating to paper mills and the paper trade in the Toscolano area,
covering the period 1460-1560, are published in Volume II of Leonardo Mazzoldi, Filigrane
di cartiere bresciane, 2 vols (Brescia: Ateneo di Scienze Lettere ed Arti, 1990-1991). Volume
I contains tracings of 1036 watermarks, with countermarks where relevant, taken from documents
mostly from the Toscolano area now in the Archivio di Stato, Brescia. The documents
in Volume II, many relating to the purchase or letting of mill sites or buildings, but also
occasionally comprising contracts between paper-makers and mill-owners or financiers,
would benefit from a careful study by an expert paper historian. Unfortunately, early mill
buildings in the area have all disappeared through modernisation or neglect, and many
sites remain unidentified. See also Ivo Mattozzi, `Il distretto cartario dello stato veneziano:
lavoro e produzione nella Valle del Toscolano dal XIV al XVIII secolo', in Cartai e stampatori
a Toscolano: vicende, uomini, paesaggi di una tradizione produttiva, ed. Carlo Simoni
(Brescia: Grafo, 1995), pp. 23-65.n.
He is not to be confused, as has happened in some prestigious recent catalogues—
such as the Catalogue of Seventeenth Century Italian Books in the British Library (London:
The British Library, 1986), Roberto L. Bruni and D. Wyn Evans, Italian 17th-Century
Books in Cambridge Libraries: A Short-Title Catalogue, Biblioteca di Bibliografia Italiana,
CXLIII (Florence: Leo S. Olschki, 1997), and the on-line catalogue COPAC—with the
poet of the same name, who lived in Tuscany from 1564 to 1639, on whom see Letteratura
italiana. Gli autori. Dizionario bio-bibliografico e indici, 2 vols (Turin: Einaudi, 1990-1991),
II, p. 1366. I wish to express my gratitude to Anna Giulia Cavagna, who kindly furnished
me with the relevant part of a forthcoming study on printing and publishing in Genoa in
the early modern period, on which much of this paragraph is based. On Peri see also Maria
Maira Niri, La tipografia a Genova e in Liguria nel XVII secolo, Biblioteca di Bibliografia
Italiana, CXLIII (Florence: Leo S. Olschki, 1998), pp. 311-318.
See Herman van der Wee, `Monetary, Credit and Banking Systems', in The Cambridge
Economic History of Europe. Volume V, ed. E. E. Rich and C. H. Wilson (Cambridge:
Cambridge Univ. Press, 1977), Chapter V, pp. 290-392; 319-322. A facsimile reprint of
Volumes I and II of Il negotiante, from the 1649 Venetian edition, was published recently
as Italian, Volume 3, of the anthology Historic Accounting Literature, Series II (London:
Pickering and Chatto, 1989-90).
![]() | Studies in bibliography | ![]() |