Pursuits of war : the people of Charlottesville and Albemarle County, Virginia, in the Second World War |
4 | ![]() | 1. |
I. |
2 | II. |
![]() | III. |
![]() | IV. |
![]() | V. |
![]() | VI. |
Government Owned Plant |
2 | ![]() | VII. |
![]() | VIII. |
![]() | IX. |
![]() | X. |
XI. |
2 | ![]() | 2. |
11 | ![]() | 3. |
![]() |
3 |
![]() | VI
Manufacturing War Goods Pursuits of war : | ![]() |
Government Owned Plant
Newest and most modern of all the Albemarle County industries
was one which was born only in the late years of the war. In the
winter of 1943–1944 the growing demand for heavy-duty tires for
trucks and planes made necessary the expansion of rayon tire cord
production. On January 12, 1944, the United States Rubber Company
decided to locate a new plant somewhere in Central Virginia.
Two days later two company officials were in Charlottesville looking
for a suitable site. When Scottsville was recommended, the U. S.
Rubber men secured the cooperation of town officials in selecting a
location just west of the town.[26]
A hitch developed when one of the landowners demanded a hundred
dollars an acre more than the U. S. Defense Plants Corporation,
which was to build this government-owned war industrial facility,
was willing to pay, but the Scottsville Lions Club agreed to underwrite
the difference, which amounted to $3,490. This obligation was
later assumed by the Albemarle County Board of Supervisors, along
with a debt of $2,623 incurred by the town of Scottsville in extending
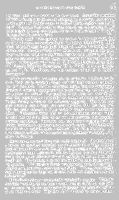
$6,944 as its share of the cost of enlarging the municipal water plant,
while a grant of $5,942 from the Federal Works Agency covered the
rest.[27] Vigorous local initiative thus secured the construction of the
third largest of seven government owned war plants built in Virginia
for operation by private firms.
Early in April, 1944, ground was broken for the new plant, and
on May 24 came a momentous day in the history of Scottsville. Hundreds
of people came from miles around to witness the laying of the
cornerstone. Governor Colgate W. Darden, Jr., welcomed the plant
to the state and called it a significant step towards achieving for Virginia
an economy in which agriculture would be balanced with industry.
Other speakers included C. T. O'Neill, chairman of the Central
Virginia Planning Commission, O. L. Ward, plant-manager-to-be,
and H. E. Humphreys, Jr., vice-president of the U. S. Rubber
Company.[28]
While construction was going on, the company, which leased the
plant from the government, began training local workers to handle
the new machines. The first employees moved into the building on
October 2, although installation of the machinery was not completed
for another six weeks.[29] The building which these new workers entered
was something new and different, a near-approach to the pushbutton
factory envisioned by industrial designers. The brick and
steel structure was a large, one-story building, 444 feet long and
264 feet wide, without a single window except in the managerial
offices. Fluorescent lights and an air-conditioning system which
changed the air every four to six minutes provided weather-proof
working conditions. Humidity and temperature controls kept the
worker comfortable and made rayon spinning easier. The floors were
designed to be resilient, absorb vibration, and resist moisture. An
ultra-modern cafeteria with a noise-absorbing ceiling was among other
attractive features.
Operation of the machinery was nearly automatic. At the push of
a button an overhead conveyor system picked up a huge half-ton
beam of rayon filament yarn, brought it to the proper machine, picked
up the empty beam, replaced it with the full one, and then rolled the
empty beam to the doorway where it could be loaded on a railroad
freight car. The filament yarn was pulled off the beam by ply-twisting
spindles. The resulting thread was respooled, twisted into high-tenacity
cord, and then woven into tire fabric. The conveyor system
finally picked up the huge roll of cord fabric and deposited it in the
storage area.[30]
This efficient process was especially valuable in wartime. With the
machines handling all the heavy work, women could do nine jobs
out of every ten in the manufacturing process and seven out of ten
in the plant as a whole. This made it much easier to recruit workers
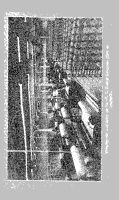

Weaving tire cord fabric in the U. S. Rubber Company plant at
Scottsville.
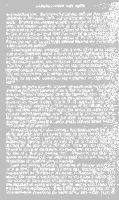
employees in November, 1944, and by Christmas was over the 200-mark.
Employment, expected to reach a maximum of 300 in March,
1945, had actually climbed to 350 by the fall of that year. The
workers toiled around the clock on a three-shift basis, six days a week.
In fact, during the spring of 1945 they kept the spindles turning for
ninety days without a stop at the request of the War Department.
Fifteen per cent of the employees received citations for not missing
a day during the period.[31]
Transformed almost overnight from a rural village to an indus
trial town, Scottsville created a Town Planning Commission to ease
its growing pains. Since the company had imported very few workers,
the housing problem was not critical. Local employees, however,
came from such great distances that the commission decided to seek
low-cost housing facilities to enable them to move nearer their jobs.
The tax structure had to be revised to pay for new civic services, including
the expanded waterworks and a proposed municipal building.[32]
Then, six weeks after the Japanese surrender, came an announcement
that the Federal government was selling the factory. The Reconstruction
Finance Corporation listed the Scottsville plant with 949
other “surplus properties” to be put on the auction block and knocked
down to the highest bidder. The R. F. C. description read like a
barren obituary: completed in 1944 at a cost of $2,400,000, affording
a total floor area of 125,500 square feet, located on approximately
sixty-six and three-quarters acres.[33] Unlisted in the inventory was
the managerial enterprise which had made equipment designed to
produce 1,200,000 pounds of cord a month turn out almost 2,000,000
pounds every month.[34]
Accomplishments like this, however, had demonstrated the value
of the Scottsville plant and saved it from the premature death which
was the fate of many a war-born industry. No less than four large
corporations tried to acquire it, with the U. S. Rubber Company
carrying off the prize for $1,837,500.[35] Since the new owner was
already in charge of the factory, the change-over was made without
the loss of a minute's working time. Albemarle's war baby had
grown to manhood and was ready to stand on its own feet in the
competition of peacetime private enterprise.
Local corporations bethought themselves of postwar planning as
early as 1944. On September 1 a seven man planning commission
was appointed by Charlottesville's mayor, J. Emmett Gleason. The
county also named a commission, and on November 3 coordination
was achieved by the selection of a three-man steering committee. This
was composed of representatives of the city, county, and Central Virginia
planning commissions. Over 2,000 questionnaires were sent to
local servicemen throughout the world asking their civilian job-preferences
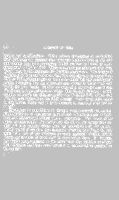
with this program reported that seventeen manufacturers in the city
and county area were employing 1,936 workers in 1944, as compared
with 1,711 in 1940. These manufacturers estimated that they
would need 2,233 employees for postwar production. The indicated
increase of 300 persons in manufacturing was expected to create from
450 to 600 additional jobs in the service industries and construction
trades, promising that the Albemarle area would be busier than ever
in the postwar world. Further evidence of a bright business future
was found in increased bank clearings. The January-February, 1946,
volume of debits for Charlottesville was $48,022,000, which was
332 per cent higher than the 1939 average. Only seven other cities
in the United States had as great increases in clearings over prewar
days.[36]
Charlottesville and Albemarle County were primarily non-industrial,
having by far the greater part of their citizens engaged in business
and professional services and in agriculture. Yet, when called
upon to help supply the Army and the Navy, the community responded
in a manner which won the appreciation of the nation.
Justly proud of the fact that Southern Welding and Frank Ix and
Sons were two of the seventeen privately operated Virginia plants
which added three or more stars to their Army-Navy “E” burgees,
the whole people rejoiced in the knowledge that together employer
and employee had kept local industry in uninterrupted production
for victory.
“Scottsville a Model for Textiles.” US.
vol. V, no. 1 (Jan.-Feb., 1946). pp.
14–17: Industrial Plant. Scottsville,
Virginia, Plancor 2136 (4 page brochure,
[War Assets Administration,
Washington, D. C., 1945])
![]() | VI
Manufacturing War Goods Pursuits of war : | ![]() |