![]() | | ![]() |
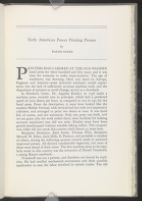
Early American Power Printing Presses
by
Ralph Green
PRINTERS HAD LABORED AT THE OLD WOODEN hand press for three hundred and fifty years, and it was time for someone to make improvements. The age of machinery was dawning. Here and there—in Europe, England, and America—some inventive mechanic would experiment, but the lack of sufficiently accurate machine tools, and the disposition of printers to avoid change, served as a drawback.
In Hartford, Conn., Dr. Appolos Kinsley, in 1796 made a machine press, entirely new in principle, which had a predicted speed of 2000 sheets per hour, as compared to 200 or 250 for the hand press. From the description, it must have looked like the modern Miehle Vertical, with vertical bed but with two impression cylinders, and arranged to print two sheets at once. It was hand fed, of course, and not automatic. Only one press was built, and we can guess why the work ended there, since facilities for making accurate machinery just did not exist. Kinsley must have been greatly handicapped without suitable inking rollers. The composition roller did not reach this country until almost 25 years later.
Benjamin Dearborn, John Sawin, Thomas Wait, Benjamin Metcalf, W. Elliot, Zach Mills, D. Pearson, and probably a number of others, during the following quarter century made or patented improved presses. All showed considerable ingenuity, but most of them were ahead of their times. The first machine press to be regularly made in this country was the invention of Daniel Treadwell, a young Boston mechanic.
Treadwell was not a printer, and therefore not bound by tradition. He had studied mechanical movements and their possible application to ease the labor involved in certain trades. The old
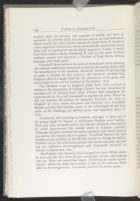
Treadwell demonstrated the press to friends and a few printers, who seemed sufficiently interested to warrant his going ahead with the manufacture of the machine. However, instead of attempting to push it further in this country, the inventor decided that England offered a larger field for the promotion of his press, and accordingly he set out for London in November, 1819.
The decision to go to England might have been arrived at owing to the experience of George Clymer, the first American to manufacture an all-iron hand press. Clymer had completed his experiments in 1813 and attempted to market his press. When he did not achieve the success he expected, however, he went to England in 1817, where his press was received very favorably. British printers had become aware of the advantages of the iron press, as the Stanhope, an all-iron press, had appeared there in 1800.
Treadwell, after arriving in London, arranged to have one of his presses built by Napier, a well-known English press builder. This took time, however, and it was the late spring of 1820 before he could demonstrate his treadle press to London printers. Although his press received favorable comment, and much interest was shown, the buyers did not appear. Treadwell blamed the lack of sales on the inability of the British printer to change his habits. Possibly one or two additional presses were built and sold, but this was not sufficient encouragement and Treadwell returned to Boston in September, 1820.
His English visit, however, had changed his views. While there, he had seen the new steam-driven newspaper presses, just coming into use. Here was something bigger, something far more revolutionary, which the American printers could not do without. Probably on the voyage home, Treadwell planned his power press.
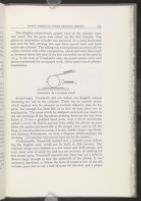
The English steam-driven presses were of the cylinder type, very much like the press now called the flat bed cylinder. The platen or impression cylinder was mounted on a fixed horizontal axis and the bed carrying the type form moved back and forth under the cylinder. The inking was accomplished automatically by rollers covered with roller composition, which had been discovered or invented about the time of the first successful use of the press in 1814. At the time of Treadwell's visit, the power presses were used almost exclusively for newspaper work, where speed was of primary importance.
Surprisingly, Treadwell did not follow the English scheme involving the use of the cylinder. There are no records extant which explain why he adopted an entirely different plan for his press, but enough has been left us so that we may piece out an explanation. The press which he designed and built was based on the old principle of the flat platen pressing down on the type form below it. It was a glorified hand press, with a lot of mechanism added to move the bed in and out from under the platen—to press down the platen automatically at the proper time—and to ink the form. It was described as a mass of levers, cranks, straps, cog wheels, and shafting. Fortunately, we have a diagram which explains the working. (All sketches reproduced here are by the author.)
Undoubtedly, Treadwell realized that a cylinder press, following the English style, could not be built in this country. The machine shops were limited to a few lathes and drill presses, and even these were of small size and not too accurate. In making his first power press, Treadwell reported that there was not a lathe in Boston large enough to face the underside of the platen. It was necessary, therefore, to follow the form of construction of the old wooden press and to use a slab of stone for the bed, and a platen
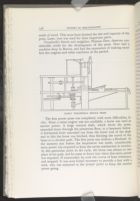
Treadwell's friend and neighbor, Phineas Dow, deserves considerable credit for the development of the press. Dow had a machine shop in Boston, and had the reputation of making excellent fire engines and other machines of the period.
The first power press was completed, with some difficulties, in 1821. Since a steam engine was not available, a horse was used as motive power. A large vertical shaft, which drove the press, extended down through the pressroom floor, to a basement below. A horizontal lever extended out from the lower end of the shaft and to this the horse was hitched, thus limiting the travel of the beast to a circular path. The first press was without a flywheel. At the moment just before the impression was made, considerable extra power was required to keep the entire mechanism in motion. At this particular point in the cycle, the horse was always at one place in his path, and he came to know just when this extra power was required. If unattended, he took the course of least resistance, and stopped. It was soon found necessary to provide a boy with a stick, who was stationed at the proper point to keep the motive power going.
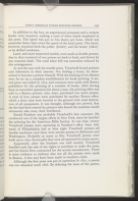
In addition to the boy, an experienced pressman and a woman feeder were required, making a total of three hands employed at the press. The speed was 500 to 600 sheets per hour, which was somewhat faster than twice the speed of the hand press. The latter, however, required both the puller (feeder) and the beater (inker) to be skilled workmen.
Later, and more improved models, were made as double presses; that is, they consisted of two presses set back to back, and driven by one common shaft. The total labor bill was somewhat reduced by this arrangement.
As was the case with his treadle press, Treadwell found printers only lukewarm in their interest. Not finding a buyer, he determined to become a printer himself. With the backing of two Boston men, he set up a complete establishment for book printing. A second press was added in 1822, and contracts were made with Boston publishers for the printing of a number of books. After having been in successful operation for about a year, the printing office was sold to a Boston printer, who, later, purchased two more presses. A total of four presses were purchased by another Boston office, which a short time later burned to the ground with total destruction of all equipment. It was thought, although not proved, that the fire had been started by printers who feared the machine would ultimately take away their livelihood.
Daniel Fanshaw was probably Treadwell's best customer. He conducted one of the largest offices in New York, since he handled the printing for the American Bible Society. At one time, twenty Treadwell presses were operating in Fanshaw's office. Isaac Ashmead of Philadelphia had at least eight Treadwell presses—all double machines—and there were similar presses in Baltimore and Washington. Probably as many as fifty Treadwell presses were built up to 1830. Eventually they were all operated by steam power.
Apparently, after the business was well started, Treadwell handled only the sale of the rights to purchase or make the press, and his friend Dow contracted for the actual manufacture. There is some evidence to indicate that not all the presses were made in Boston. A few may have been made in southern cities.
Although the first press was put in operation in 1821, a patent was not obtained until 1826. By delaying the issue of the patent,
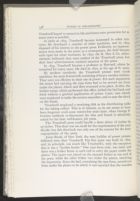
As early as 1825, Treadwell became interested in other ventures. He developed a number of other machines, and in 1829 disposed of his interest in the power press. Evidently, no improvements were made in the press; as a consequence, the field became wide open for other inventors. In 1830, the R. Hoe & Co. advertisement indicated they were makers of the Treadwell press, but their later advertisements omitted mention of the press.
In 1835, Treadwell became a professor at Harvard, where he remained for many years. He died in 1872, at the age of 81 years.
By modern standards, the Treadwell presses were crude machines, the main framework consisting of heavy wooden timbers. They were not efficient in their use of power. For each impression the entire bed carrying the type form had to be moved out from under the platen, inked, and then returned to its place. At first, the leather straps, which performed this office, jerked the bed back and forth without a gradual application of power. Later, cam wheels were employed to make the motion smoother, and to ease the shock on the frame.
Treadwell employed a revolving disk as the distributing table for the inking rollers. This is of interest, as its use seems to have been forgotten until some twenty-five years later, when George P. Gordon suddenly re-discovered the idea and found it admirably suited for his later well-known job press.
The Treadwell press could handle a sheet about 18 inches by 23 inches. This sheet was too small for the requirements of the next decade, but this drawback was only one of the reasons for the later unpopularity of the press.
Jonas Booth, of New York, the next builder of power presses, followed soon after Treadwell. His first press was built in 1822, and, in principle, was much like Treadwell's, with the exception that it was a "double feeder." One type form only, was used, and there was a frisket frame at each end to carry the paper under the platen. The paper was placed on the exposed frisket at one end of the press, while the other frisket was under the platen, receiving the impression. Since the bed, containing the type form, moved out from under the platen to be inked, it was reported that the wooden
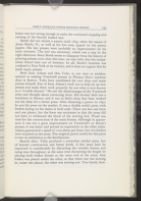
Booth did not obtain a patent until 1829, when the names of Jonas Booth, Sr., as well as his five sons, appear on the patent papers. His last presses were probably an improvement on his early ventures. The bed was stationary, which was a step in the right direction. Since Booth seems to disappear from the history of printing presses soon after this time, we may infer that the competition forced him out of business. In all, Booth's business was confined to New York or its vicinity, and it does not appear that he made many presses.
Both Isaac Adams and Otis Tufts, at one time or another, assisted in making Treadwell presses in Phineas Dow's machine shop in Boston. Tufts later established his own shop and made presses himself. Part of Isaac Adams's work was to help set up new presses and make them work properly: he was what is now known as a "trouble shooter." He saw the disadvantages of the Treadwell press and thought about correcting them. His brother Seth was a machinist in Boston, and it was in Seth's shop that Isaac worked out his ideas for a better press. After obtaining a patent in 1830, he put his press on the market. It was a double ended press, with feeders laying on the sheets at both ends. There was but one form and one platen, but the form was stationary so that the press did not have to withstand the shock of the moving bed. Wood was used for the construction of the main frames. Although in appearance it was not a great improvement on Treadwell's or Booth's presses, it was faster and proved its superiority to the older styles. Adams guaranteed a speed of 1000 sheets per hour, but two feeders were required at the press. The original patent model for this press is now on exhibition at the Smithsonian.
Shortly after, Tufts produced a somewhat similar press, but of heavier construction and better finish. A few years later he improved it considerably by discarding the wooden frames and using iron throughout, at the same time shortening the length by placing both frisket frames at the same end of the press. One frisket was placed under the other, so that when one was moving in, under the platen, the other was moving out. Two hands, however,
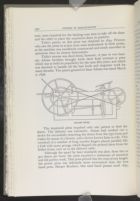
Tufts's patent on this press was obtained in 1834. Printers who saw the press in action were most enthusiastic in their praise, as the machine was excellently constructed and much smoother in operation than its clumsy forerunners.
Tufts's success was short-lived, however. A year or two later, the Adams brothers brought forth their final attempt—a press which was to hold its popularity for the next fifty years, and which was destined to handle all the best book and magazine work for many decades. The patent granted to Isaac Adams was dated March 2, 1836.
The improved press required only one person to feed the sheets. The delivery was automatic. Adams had worked out a device for successfully removing the sheets from the type form and frisket by means of a blower, and a device known later as a fly. This consisted of a number of long wooden fingers placed parallel, like a fork with many prongs, which flapped the printed sheet from the frisket frame over on to the delivery table.
Although the speed by later standards was slow, from 600 to 900 sheets per hour, the press required a minimum of attention and did perfect work. This press proved that for runs of any length, the power press was definitely more economical than the iron hand press. Harper Brothers, who used hand presses until 1837,
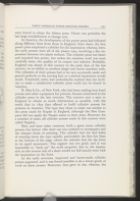
In America, the development of the power press had followed along different lines from those in England. Over there, the first power press employed a cylinder for the impression; whereas, here, the early presses were all of the platen type, involving a flat impression between two plane surfaces. The cylinder press was faster and required less power, but unless the machine work was most carefully done, the quality of its output was inferior. Probably, England was ahead of this country in the early days of the last century, in its ability to produce larger and better machine tools. The cylinders of their presses had to be very accurately made and geared perfectly to the moving bed, or a slurred impression would result. Treadwell, early, had undoubtedly realized that the facilities to make a satisfactory cylinder press could not be found in America.
R. Hoe & Co., of New York, who had been making iron hand presses and other equipment for printers, became interested in the cylinder press in the late twenties. The concern sent a man to England to obtain as much information as possible, with the result that in 1832 they offered to build cylinder presses for printers in America. The type they chose to make was similar to the press made by Napier in England, although the Hoe Company did not apply the Napier name to their press. However, for a number of years, all cylinder presses made in this country were called Napiers.
Hoe, and later other concerns, built a great many cylinder presses, but before 1860 their use was confined to newspapers and the cheaper kinds of printing. The cylinder had the bad habit of wearing down the type rapidly, particularly the first few lines at the bottom of the page, where the cylinder first hit the form in its rapid movement. The register was not good, and it was impossible to "back up" the work properly; that is, the impression on the reverse side of a sheet would not fall exactly even with the impression on the front.
In the early seventies, improved and better-made cylinder presses appeared, and it was found possible to do a better grade of work on these presses. Moreover, they grew in size, whereas, the
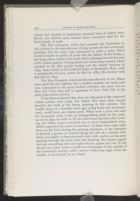
The Hoe Company, which had assumed the leadership in this country in the manufacture of large presses for fast newspaper printing, had for some time attempted to make a press which would compete in quality of work with the Adams. In the forties, a few large platen presses were built which infringed certain features of the Adams patents. A long drawn out controversy ensued, which resulted in the Hoe people buying out the Adams business in 1859. Isaac retired to his boyhood home in Sandwich, Mass., with a considerable fortune, where he died in 1883. His brother Seth had died in 1873.
The Hoe Company continued the manufacture of the Adams press until the late eighties, but a smaller number was made each year. Compared to the more modern cylinders, the press was too slow, but a few were still in operation in New York City in the early years of this century.
It has been estimated that over one thousand of the improved Adams presses were made. For almost fifty years these presses handled the bulk of the better printing in this country. The smaller shops of a hundred years ago, doing book and newspaper work, would have one Adams press. When such a press was used for newspaper work, it left its distinguishing mark on the make-up of the page. In order to lift the sheet from the form after printing, the frisket frame contained one or more longitudinal wires, which supported the center of the sheet. As these wires came right down on the form during the printing operation, it was necessary to provide a groove or channel along one side of a column rule, about one-eighth to three-sixteenths inch wide, and to cut the same opening through the head rules and heading. Six-column papers had one supporting wire and eight-column papers had two. If one should ever come across a small-town newspaper of the middle of the nineteenth century, with a narrow white strip right down the middle, it was printed on an Adams.
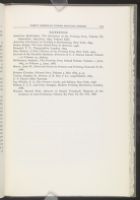
REFERENCES
- American Bookmaker, The Evolution of the Printing Press, Volume XI, September, 1890-June, 1892, Volume XIII.
- American Dictionary of Printing & Bookmaking, New York, 1894.
- Green, Ralph, The Iron Hand Press in America, 1948.
- Hansard, T. C., Typographia, London, 1825.
- Hoe, Robert, A Short History of the Printing Press, New York, 1902.
- Journal of the Franklin Institute, Abstracts of U. S. Patents Issued, Volume 1 to Volume 13, 1826-32.
- McNamara, Stephen, The Printing Press, Inland Printer, Volume 1, June, 1884, to Volume 4, June, 1887.
- Moore, John W., Historical Notes on Printers and Printing, Concord, N. H., 1886.
- Printers Circular, Phineas Dow, Volume 4, May 1869, p. 91.
- Tucker, Stephen D., History of R. Hoe & Co., unpublished, 1885.
- U. S. Patent Office Records.
- Van Winkle, C. S., The Printers Guide, 3rd Edition, New York, 1836.
- Wilson, F. J. F., and Grey, Douglas, Modern Printing Machinery, London, 1888.
- Wyman, Morrill M.D., Memoir of Daniel Treadwell, Memoirs of the Academy of Arts & Sciences, Volume XI, Part, VI, No. VII, 1888.
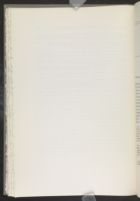
![]() | | ![]() |