![]() | Parkways and park roads | ![]() |
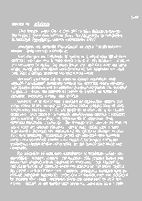
LECTURE 12 - PAVEMENTS
(See Seelye, pages 343 to 345, 370 to 382; Thickness Design,
The Asphalt Institute, College Park, MD; Interim Guide for Design
of Pavement Structures, AASHTO, Washington, D.C.)
Pavements are flexible (bituminous) or rigid (reinforced concrete).
Each has its attributes.
Concrete has the advantage of acting as a rigid slab which distributes
the load over a wider surface area on the subgrade. Because
the structure is rigid, the wheel loads are supported over the occasional
voids and soft spots that develop in the subgrade; the slab
acts like a bridge spanning the underlying voids.
Concrete pavements can be built to closer tolerances than
asphalt (bituminous) pavements because the formwork which contains
the plastic concrete can be accurately installed before the material
is poured. Also, the mixture is easier to control in terms of
hardness, strength, curing, and testing.
Concrete is by definition a mixture of aggregates, cement and
water which in the process of hydration forms a rigid mass of high
compressive strength. It is the property of concrete to be "incompressible"
that makes it a valuable construction material; furthermore,
concrete has a very low coefficient of expansion which
provides structural stability. The problem with concrete is that it
has a very low tensile strength: steel rods, which have a very
high tensile strength are implaced in the concrete mixture to provide
that property. Expansion joints are designed into concrete
structures to control cracks that result from tensile weakness;
otherwise, random cracks would occur as the heated slab cools and
contracts.
The selection of aggregate contributes to hardness, color, and
durability. Crushed granite, for example, will produce harder concrete
than crushed gravel composed of sandstone. The angularity
and distribution of particle sizes are factors of hardness; angular
particles (crushed stone) have a greater mechanical strength than do
rounded particles (gravels). Particles of uniform size are separated
by uniform size voids; graduated sizes are introduced to fill the
voids. Cement is the binder that locks the particles into a mass.
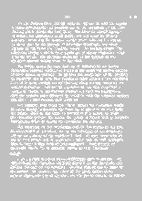
We are finding that calcium chloride applied to melt ice causes
a rapid deterioration of concrete due to the oxidation of the reinforcing
steel within the road slab. The concrete itself appears
to slough, the aggregates break apart, and the steel is finally
exposed. According to concrete people whose opinions I respect,
it seems that in the process of oxidation (rusting), the metal
expands to ten times its original volume. As rusting occurs, the
concrete, having a low tensile strength, is slowly "exploded" away
from the steel. The external crumbling is the symptom of the
interior process taking place in the slab.
The bridge decks you have seen being replaced on the George
Washington Memorial Parkway at Dead Run and Spout Run failed because
of this oxidation process. To prevent the recurrence of the problem
an apparatus was to have been installed which causes a low electrical
current to pass through the reinforcing steel thereby stopping the
oxidation process. The bridge engineers of the FHWA described a
technique tested by the Germans wherein the slab was impregnated
with hot asphalt under pressure in order to seal the concrete against
moisture. I know nothing more about it.
The concrete road slabs are "tied" across the expansion joints
by steel dowels to overcome the tendency of one slab to rise above
the other. Half of the dowel is covered with a sleeve to allow
for expansion between the slabs; the joint is filled with an asphalt-impregnated
fiber or mastic to waterproof the opening.
The thickness of the reinforced slab is determined by the anticipated
weight of vehicles, and by the stability of the subgrade,
and by the quality of the concrete itself. In some situations it
may be more economical to construct a thick slab of soft aggregate
than to build a thin slab of hard aggregate. Availability of
materials can be the determining factor in slab thickness.
CURBS:
I am a strong believer in mountable-type curb 'n gutter. The
curb retains the shoulder, controls drainage on the pavement, and
defines the edge of the pavement. Colored pigment can be added to
the concrete to resemble the color of the local soils; also,
colored aggregates can be selected and the finish exposed to resemble
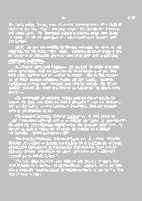
added to the mix. Don't use lamp black! It weakens the concrete
and looks ugly. Use inorganic pigments; colors range from black
to buff. Or use an aggregate of proper color...it makes a good
job better.
NOTE: If you are working on defense roadways, be aware of the
requirements for heavy wheel loads. Haunches or grade beams might
be required at expansion joints, especially over soft subgrades.
BITUMINOUS PAVEMENTS:
Bituminous pavements (asphalt) are cheaper to build than concrete
pavements; they are more costly to maintain over the long
haul (time period) but are easier to repair. The riding surface
is smoother because expansion joints are not needed. However,
chuckholes develop with freezing and thawing action. The black
surface resists ice formation but it is vulnerable to damage from
gasoline.
The advantages of concrete versus asphalt can be argued by
people who know more about it than I do...but I like the Colonial,
and the Suitland, and the Baltimore-Washington Parkways because
it's my prejudicial nature.
The Asphalt Institute defines Asphalt as, "A dark brown to
black cementious material solid, semisolid, or liquid in consistency,
in which the predominating constituents are bitumens which occur in
nature as such or which are obtained as residue in refining
"petroleum." (ASTM Designation D8)
The Asphalt Institute defines Bitumen as, "A mixture of hydrocarbons
of natural or pyrogenous origin, or a combination of both;
frequently accompanied by nonmetallic deriviatives which may be
gaseous, liquid, semisolid, or solid; and which are completely
soluble in carbon disulfide."
The key words indicate that asphalt may contain bitumen, and
that bitumen is a mixture of hydrocarbons. Asphalt, then, is that
black semisoft material mined in Venezuela which we use to mix with
oil to make a road.
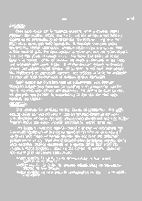
SURFACING:
Most park roads are bituminous concrete over a crushed stone
subbase; the surface course may be a cold mix or hot sheet asphalt
depending on availability of materials and climate. Big Bend has
much heat, sand, and hard aggregate; Yellowstone has much cold,
travertine, little aggregate. Crushed stone chips are apread over
a tack coat to give the road surface a color and texture which blends
into the immediate landscape hues. The South Rim Drive at Grand
Canyon is surfaced with red chips; the roads at Craters of the Moon
are surfaced with black chips. I prefer crushed gravel to rounded
gravel (of uniform size) because it adheres to the tack coat longer.
The angularity of particles exposes more surface area to be enclosed
in road tar than is enclosed in rounded gravel particles.
Last summer our Park Engineer in Yellowstone used Asphalt
Emulsion rather than road oil in applying a chip seal; the reason
being the high cost of oil and gasoline. It worked as well as oil,
we thought, and it will be interesting to see how the road came
through the winter.
THICKNESS:
The subgrade is critical in the design of pavements. The Soil
Manual which Rob McLeod gave to you in Terrain Analysis contains
a description of tests for soil properties; you'll see the California
Bearing Ratio and other testing procedures. Check those out.
The Asphalt Institute has developed a method of estimating the
necessary thickness of pavements based on traffic volumes equated
to truck axle loads of 18,000 pounds; you can find the detailed
explanations in the Institute's publication, Thickness Design, MS-1.
They classify traffic according to a system which they call IDT
(Initial Daily Traffic). That is the volume of traffic expected
the first year following completion:
Light traffic is up to 1,000 vehicles/day on two-lanes;
equates to 10 trucks.Medium traffic is 1,000 to 100,000 vehicles/day on two-lanes;
equates to 100 trucks.Heavy traffic is over 100,000 vehicles/day on two-lane or multilane
roads.
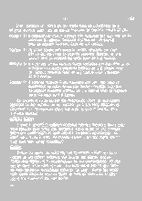
Four examples are given in the text; each is calculated on a
20-year service life, and an annual increase in traffic volume of 3%.
Example 1: A residential street carries 400 vehicles per day, CBR is 4;
requires an Asphalt Concrete Surface of 1.0 inches
over an Asphalt Concrete Base of 5.0 inches.
Example 2: An urban Interstate carries 10,000 vehicles per day;
CBR is 10; requires an Asphalt Concrete Surface of 2.0
inches over an Asphalt Concrete Base of 6.5 inches.
Example 3: A suburban street carries 4,000 vehicles per day; CBR is 3;
requires an Asphalt Concrete Surface of 1.5 inches over
an Asphalt Concrete Base of 4.5 inches over a Subbase
of 8.0 inches.
Example 4: A Parkway carries 8,000 vehicles per day; the road is
restricted to cars, buses and service trucks; requires
an Asphalt Concrete Surface of 1.0 inches over an Asphalt
Concrete Base of 6.0 inches.
An alternate is given for the Interstate where an equivalent
pavement is 2.0 inches, on 4.0 inches, on a 5.0 inch subbase; an
alternate for the Parkway shows 1.0 inches, on 4.0 inches, on a
5.5 inch subbase.
ASPHALT CURBS:
I have a prejudice against extruded asphalt curbs; I don't like
them because auto tires and snowplows leave scars on the surface.
Often the workmanship is poor and the alignment is crooked. Al
Kuehl used to call them "toothpaste curbs"...he was right and is
very much part of my prejudice!
TRAILS:
Before we leave the subject, let me strike a blow for soil-cement
as the better material for hiking and biking trails!
Bituminous surfacing is out-of-place in the backcountry! If you
use it there, I'll hunt you down and make you clean-it-up! Even
on road surfaces, bituminous material is ugly. Cover the stuff
with stone chips or bury it under an inch of dirt...it belongs
under the road surface, not on it.
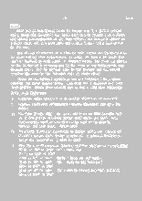
MIXES:
Road mix is bituminous concrete prepared with a patrol grader
and a spray rig alongside the road; cold mix is prepared in a plant
and spread and compacted at air temperature; hot mix is prepared in
a plant where oil and aggregate are heated before being hauled hot
to the job.
Oil (Bitumen) becomes more viscous with higher air temperatures;
at Death Valley with temperatures of 120+, oil runs like water and
must be blotted-up with sand! At Furnace Creek, the road oil flowed
to the bottom of a vertical sag in the road to the maintenance and
housing area. Try to explain that to the mothers and the school
teacher who stop by the job with fire in their eyes!
Write to the Asphalt Institute and the Portland Cement Association
for their publications. And send for a publications list
from AASHTO. Start your library now...it's a long time building!
BITUMINOUS MATERIALS:
Requires soils analysis to determine thickness of pavement.
Asphalt Institute establishes various thickness and spec for
soils.Low Type Bituminous: for wheel loads up to 7000 pounds; life
up to two years; requires annual seal coat; low cost, high
maintenance; surface treatment less than 1″ thickness;
"prime and seal coat: Armor coat"Calculate thickness according to Seelye table for "design of
flexible pavements"; design curves are by Asphalt Institute;
soils are classified by USDA or USCESelection of Bituminous Material depends largely on temperature!
RT-1 is 60° to 125° (RT = Road Tar) RT-12 is 175° to 250° RTCB is 60° to 120° (RTCB = Road Tar Cut Back) SC-0 is 50° to 120° (SC = Slow Curing Road Oil) SC-6 is 400° to 400° MC-0 is 50° to 150° (MC = Medium Curing Cut Back Asphalt) MC-5 is 200° to 275° 7RC-0 is 60° to 125° (RC = Rapid Curing Cut Back Asphalt) RC-5 is 200° to 250° SS-1&2 is 50° to 120° (SS = Slow Setting Asphalt Emulsion, AE) MS-1 is 60° to 120° (MS = Medium Setting Asphalt Emulsion, AE) RS-1 is 80° to 135° (RS = Rapid Setting Asphalt Emulsion, AE) Asphalt Cement Penetration is hot application from 275° to 400°
(the higher the number the more viscous the material)Types of Pavement:
1.
2.
3.
4.
5.
6.
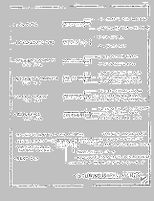



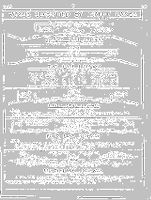

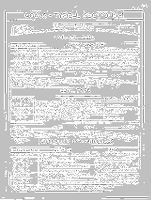

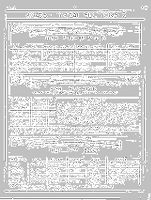

![]() | Parkways and park roads | ![]() |