Machine Shops
Among the heavier industries the Southern Welding and Machine
Company provided a rags-to-riches success story in the best Horatio
Alger tradition. The firm began in the depression thirties with little
capital other than the ingenuity and enterprise of its two partners,
R. R. Harmon and J. Tevis Michie. Its first plant was a small, abandoned
building, which leaned at a tired angle, and its first order
brought in only twenty-five cents. With no regular products of its
own, the firm became a custom foundry and machine shop, taking in
whatever business it could locate. When orders were slow, Harmon,
who was plant manager, worked on his special interest, experimental
models of gas purification and combustion equipment, and acquired
a number of patents in the process. Whatever profits were made were
devoted to the expansion of the shops and the purchase of discarded
machinery, which was moved in and put back into condition.
By 1939 this careful management had expanded the operation to
twenty-five employees and an annual business of $50,000. The next
summer brought the company its first defense order, a contract to
produce electrical stuffing tubes for the United States Coast Guard.
These tubes were used to conduct electrical wiring through bulkheads
—“partitions,” in landlubber language. The success of this initial
contract soon brought follow-up orders from the Navy, the Maritime
Commission, and private shipbuilders. Tens of thousands of
these tubes were delivered at prices well below the cost which the Navy
had established on the basis of its own production.
Another early order came as a result of the Harmon patents. To
expand the nation's output of sulphuric acid it was decided to convert
the Ducktown, Tennessee, plant of the Tennessee Copper Company
from the chamber process to the contact acid process. Gas purification
equipment controlled by some of Harmon's patents was selected
for use in the new plant, and his firm designed, built, and
supervised the installation of the equipment. This was the first time
that a wet process for purifying roaster gases for sulphuric acid production
had ever been used. The Charlottesville equipment proved
much superior to the apparatus it replaced, and its increased yield of
sulphuric acid helped to make possible the vast expansion in the
nation's output of TNT which followed.
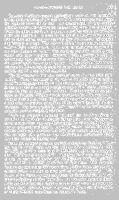
Southern Welding's greatest achievement, however, was its contribution
to the building of the vast carrier fleet which eventually swept
the Japanese Navy off the seas. An essential part of these mobile
airfields is a device for halting the planes as they come in for a landing.
When the ship's aircraft are in the air, a series of cables are stretched
across the flightdeck. A hook in the tail of a landing plane grasps
one of these cables, and the resulting drag slows down the aircraft
and brings it to a stop. The cable is a part of a complicated assembly
called a flight-arresting gear, which must be constructed to have just
the right amount of “give.” Too much or too little elasticity may
injure both plane and pilot. Southern Welding proved so adept at
constructing these delicate mechanisms that the company was given
the task of outfitting scores of carriers. At one time in 1943 it was
working on flight-arresting gears for forty-five different carriers being
built by the Navy and private shipyards.
The Charlottesville firm also provided many flat-tops with crash
barriers. These were raised at the end of the flight deck to keep a
plane from toppling into the sea when the arresting gear failed to halt
it, and they had to be strong enough to stop a dive-bomber careening
across the deck at sixty miles an hour. Another carrier device produced
by Southern Welding was the spotting dolly. This was a four-wheeled
mobile jack, which lifted the planes and moved them about,
simplifying the problem of parking in the narrow spaces of the carrier
hold. One more product for naval aviators was the bridle-catcher
assembly used on catapult mechanisms.
While the company was going “all out” for the Navy pilots, it
somehow managed also to produce for the Army such miscellaneous
items as caps, bases, and nose-closing plugs for 90-pound fragmentation
or anti-personnel bombs; hydraulic control devices for flying
bombs; bomb band trunnions for 500-pound bombs; trail casters for
gun carriages; gun platforms for 40-millimeter anti-aircraft guns;
and trick wheels for landing craft.
Some idea of the changes this production meant for Southern Welding
can be gained from the fact that its sales mushroomed from
$67,000 in 1940 to more than $1,000,000 in 1943, an increase of
about 1,900 per cent since 1939. The plant itself more than tripled
in area between Pearl Harbor and the Japanese surrender, growing
from 16,000 to 53,000 square feet of floor space. The expanded
facilities included a large fabrication shop, a boiler house, and a private
railroad siding, all built in large part of salvaged materials. The
trusses of the fabricating shop came from the dismantled Sixth Avenue
Elevated Railway in New York City, and the only items the Chesapeake
and Ohio Railway supplied for the siding were the switch and
a signal light. New equipment was brought in at a cost of $72,000,
of which $43,000 came from the company's funds.
This rapid expansion placed a severe strain on working capital.
Money to pay wages and bills for raw materials had to be borrowed
from a local bank until payment arrived for completed contracts.
Growing with mounting inventories, the loan eventually reached ten
per cent of the bank's deposits, the legal maximum for a single loan.
Additional funds then had to be secured through the Federal Reserve
Bank, with the Navy guaranteeing repayment. Raw materials were
often as hard to find as money. While the firm had top priorities,
this meant merely the right to buy the material if it could be located.
Nevertheless, the company usually managed to get its deliveries
through on time and never caused an important delay in production.
Southern Welding's biggest problem, however, was recruiting and
training its labor force. Employment jumped from 25 in 1939 to
a peak of 204 in 1943, but it proved impossible to hold this many
workers under wartime conditions. Forty-eight employees left to
enter the armed forces. Training the industrial recruits required managerial
ingenuity. When the company took on the crash barrier contract,
it discovered that its new and unskilled workers could not read
the blueprints. The management went to work and produced a set
of drawings of a different and more readily understandable type. Delighted
with the results of this initiative, the Navy incorporated the
drawings into a manual for use aboard all carriers on which this type
of crash barrier was installed.
While producing vital war materiel, the Southern Welding and
Machine Company earned the right to fly the U. S. Treasury Department
Minute Man Flag and the Army-Navy “E” burgee with three
white stars. When the first award of the Army-Navy “E” was announced
in January, 1944, J. Tevis Michie remarked that “all credit
must go to our employees for the splendid job they have done on war
contracts.” The presentation of the “E” flag was made in the company's
fabrication shop on February 26 by Captain Edgar M. Williams,
U. S. Navy, the commanding officer of the V - 12 unit at the
University of Virginia. At the same time Brigadier General E. R.
Warner McCabe, U. S. Army, commanding officer of the School of
Military Government, presented award pins to each of the company's
employees. Stars signifying continuing outstanding excellence in war
production during subsequent six-month periods were added on July
24, 1944, January 29, 1945, and September 1, 1945.
The company's problems after V-J Day exceeded anything which
had been experienced in the hectic days of the war. When a nationwide
strike of steel workers in January, 1946, threatened to shut off
the firm's supply of its chief raw material for postwar production of
bulldozers, road scrapers, earth movers, food processing equipment,
and other custom-built appliances, 88 out of 103 employees joined
the two partners of the firm in denouncing federal labor policies which
permitted such a strike to occur. Their protest and constructive criticism
took the form of an open letter to the President of the United
States which was published at their own expense in a full-page advertisement
in the local newspaper. Copies of it were sent to Virginia
delegates in Congress as well as to the President. The threatened
shut-down, following an unavoidable slow-down, materialized in February,
1946, and lasted two weeks. Soon after steel could be
obtained again, the company had secured sufficient orders to justify
increasing the work week from forty hours to fifty-four. With the
lifting of the Federal lid on wages, three general wage increases were
voluntarily instituted. Although business was well below the wartime
peak, it was still more than four times the average of 1939, indicating
that this infant industry had grown to maturity.
[20]
Another metal-working firm, N. W. Martin and Brothers, continued
its peacetime production of roof and sheet metal through 1942.
Its output was used in the construction of Camp Lee, Fort Belvoir,
and the Woodrow Wilson General Hospital near Staunton, Virginia.
In 1943, however, the firm took an entirely new line, the molding of
plastics, when it received a contract to make noses for Black Widows.
The nature of this work was a well-guarded secret for several years
until military developments permitted the Army to release the story
of its deadly night fighter. Making plastic noses for the plane should
have presented a problem for sheet-metal workers, but Martin and
Brothers earned the commendation of the Air Technical Service Command
for the way in which they handled the job. Instead of waiting
for the necessary new equipment to arrive, the firm set to work to
produce the machinery in its own shops. At the same time employees
were trained in the new processes so that equipment and workers were
ready to start the job simultaneously. This enterprise enabled the
Martins to turn out noses for two thousand Black Widows.[21]
[20]
W. Edwin Hemphill, “The Saga of a
Machine Company,” The Commonwealth,
vol. XIV, no. 1 (January,
1947), pp. 5–7. 24. See also War Manufacturing
Facilities Authorized
Through December, 1944. vol. II, p.
627; Progress, Jan. 25, Feb. 25, 1944,
Jan. 29, Sept. 1, 1945, Jan. 24, 28,
Feb. 4, 1946
[21]
Progress, Feb. 27, 1945