![]() | University of Virginia record February, 1914 | ![]() |
LABORATORY WORK IN STEAM ENGINEERING.
The Steam Engine Tests are made on the high-speed Ball
engine, which operates the shops. This motor has been specially
equipped for the purpose. It receives steam from the main line
through a Sweet separator; humidity determinations are thus made
twice—once by a separating calorimeter before the steam enters
the separator, and again by a throttling calorimeter as it enters the
cylinder. It is fitted with proper indicators, and permanent indicator
rigging so that at any time cards may be taken and the indicated
horse-power determined. In like manner a rope friction brake
is so arranged that it may be at once applied for the determination
of brake horse-power. Connections are so made with a Wheeler
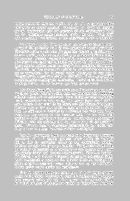
condensing or non-condensing. Provisions are made for measuring
the temperatures and the amounts of the condensation water
and the condensed steam produced during the run. With these
data a complete heat balance of the experimental run is attainable.
The Steam Turbine Tests are made on a DeLaval 30 horsepower
turbine direct connected to a 25 kva. alternating current generator.
The turbine takes steam from the main line through a Cochrane separator;
humidity tests are made with a throttling calorimeter below
the separator. Pressure guages indicate the steam pressure before and
after passing the governor and after expansion in the nozzles. Humidity
tests of exhaust steam are made with a separating calorimeter
The turbine has interchangeable nozzles for saturated steam exhausting
to atmosphere; for saturated steam exhausting to condenser;
for superheated steam exhausting to condenser. Steam consumption
is determined by weighing the condensate. Power output is measured
at the generator, the efficiency of the latter being known.
The Steam Pump Tests are made on a Worthington direct acting
duplex pump, receiving steam from the main line and exhausting
either to atmosphere or condenser. By weighing the condensed steam
hourly consumption is determined. The pump draws water from a
concrete tank in the floor of the laboratory and delivers it to a copper-lined
tank in the attic under a head of forty-five feet. Water
from the attic tank is returned to a wrought iron weir tank in the
laboratory, and thence to the concrete tank. In the weir tank
quantity of water delivered is measured. Velocity head is determined
indirectly from the quantity and the known area of the discharge
nozzle. Friction head is determined independently, and steam consumption
per developed horse-power-hour is computed.
The Air Compressor Tests are made on a Remington Ammonia
compressor, 4″ × 6″ double cylinder, single acting, so arranged
that it may be connected either to the refrigerating machine
or an air storage tank of ample capacity. Temperature of the storage
tank is determined at a thermometer cup passing well across
the diameter of the tank near its central portion. From the temperature,
pressure, and the known capacity of the tank compressor capacity
is determined; a check on the capacity from the indicator diagrams
being thus obtained. Power input is measured by a calibrated
electric motor which drives the compressor.
The Air Engine Tests are made on a 3″ × 4″ single cylinder
double acting engine receiving air from the storage tank at any desired
pressure below 100 lbs. The engine is permanently rigged
for taking indicator diagrams, the intake air temperature being determined
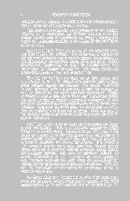
provide means for determining power output.
This equipment provides for the determination of (a) Mechanical
efficiency of the compressor, (b) Cylinder efficiency of the compressor,
(c) Efficiency of transmission, (d) Cylinder efficiency of the
engine, (e) Mechanical efficiency of the engine, (f) Over-all efficiency
of the air plant.
For Steam Boiler Tests the boilers of the university heating
and lighting plant are available. The department is equipped with
the necessary apparatus—thermometers, gauges, steam calorimeters,
fuel calorimeters, gas analyzers, scales, tanks, and so on. Students
of Mechanical Engineering are taught by practical lessons in the
boiler room the standard methods for boiler trials, and the class
makes each session at least one complete trial.
The Gas Engine Tests are made on an Otto machine of 15
I. H. P. and 12 B. H. P. This is also provided with its friction
brake, indicator rigging, and indicator. The cooling water is run
in from calibrated tanks and provision is made for observing not
only its amount but the initial and final temperatures. Gasoline
or alcohol is used as fuel, and is run in from a graduated wrought-iron
bottle, so that the amount consumed is determined. The heating
power is obtained by an independent test with a Rosenhain calorimeter.
Samples of the burnt gases are drawn from the exhaust
pipe and analyzed in an Orsat gas apparatus. With these data, and
the observed numbers of revolutions and explosions, the heat balance
is worked out.
The Refrigerating Tests are made on a Remington Ice Machine
of one ton capacity. This is an ammonia compression machine
driven by an electric motor. Instead of brine, plain water is used,
heated by a steam jet to 100 degrees and then cooled down to 40
degrees by the machine. A run is first made with the pipes empty
in order to determine the friction horse-power. The ammonia is
then turned on and the run is made under load. In both cases the
power consumed is measured both by wattmeter and by ammeter
and voltmeter readings. The tanks are accurately calibrated and
careful measurements of the temperature are made through the
run. Indicator cards are also taken from the ammonia cylinders
and the number of revolutions is registered by counter. With these
data the mechanical and thermodynamic performance of the machine
are figured out.
For Engine Balancing Experiments the 3″ × 4″ air engine is provided
with detachable weights which may be clamped at any desired
position relative to the crank and the axis of the main shaft. The
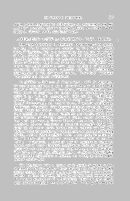
from previously computed weights being determined by the
nature of vibration of the suspended frame.
![]() | University of Virginia record February, 1914 | ![]() |